Disclaimer: As an Amazon affiliate, I may earn a small percentage from qualifying purchases. This is at no extra cost to you. Learn more here.
A lathe machine is a very useful tool for metal or wood shaping. Some of these operations include threading, drilling, and boring.
These are essentially cutting tools and high-speed rotating workpieces mounted on tool posts. The workpiece is what rotates about a vertical axis while a stationary cutting tool works on it.
There are different kinds of lathes that specialize in various materials and techniques — such as the turret lathe, engine lathe, and capstan lathe.
But in this article, I’ll be talking more in-depth about turret lathes.
Key Takeaways
- A turret lathe machine is a modified conventional metalworking lathe, making it ideal for mass production.
- Turret lathes can be classified in different ways — such as by size, method of control, and bed orientation.
- A turret lathe can sometimes be confused with a capstan lathe and an engine lathe, though these three all differ from one another.
What Is a Turret Lathe?

A turret lathe is a metalworking lathe machine used in the repetitive production of duplicate parts.
It allows multiple cutting operations to be done quickly and easily in succession, making production more efficient.
This is thanks to the turret, which is an indexable tool holder that lets you switch tools WITHOUT needing to install and uninstall them (as opposed to a conventional turret).
FUN FACT: The very first turret lathe was built in 1845 by Stephen Fitch. However, the first fully automated turret lathe wasn’t until 1873, thanks to Christopher Spencer.
Different Parts of a Turret Lathe
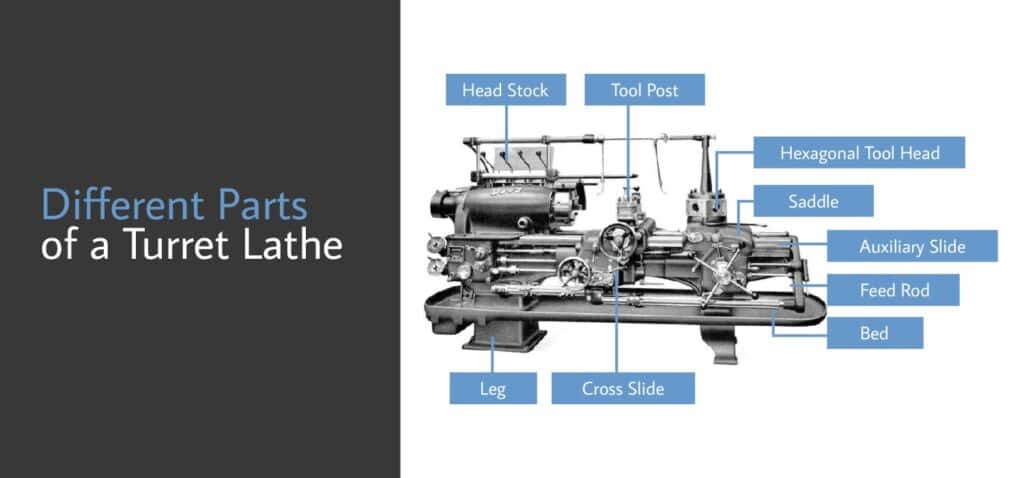
The turret lathe has multiple parts. But below, I’ll only be talking about a few of the more important ones:
Turret
Of course, the reason this machine has its name is the existence of a turret.
The hexagonal turret head can hold six different tools and can be rotated manually. Each of its six faces has four tapped holes where you screw attachments in place.
Aside from that, the saddle can be moved nearer or farther from the workpiece.
Cross-Slide
Also called the carriage, the cross-slide is found between the tool post and saddle and can move perpendicularly to the saddle.
This unit is further divided into four more parts:
- Cross-slide
- Square turret
- Carriage
- Apron
The cross-feed dial on the carriage is great for very accurate work since it’s divided into HUNDREDTHS of millimeters marked with a clip. This lets you keep cutting by hand feed until trip dogs disengage the power feed.
Headstock
The headstock is where you can find all the controls of the turret lathe — such as start, stop, and speed control.
Perhaps it can also be said that the main feature of the headstock is its ability to let you further “customize” your cutting, so to speak. That’s because you can also control rapid stopping, starting, and speed changes.
There are two types of headstocks according to the type of drive system you have:
- Electric headstock – Here, the spindle speed depends on the electric motor speed, giving you better speed control. It’s good when you’re working with small workpieces.
- Geared headstock – With this type, you control the spindle speed by controlling the torque, which is INDIRECTLY proportional. This is ideal for larger workpieces.
Driving Clutch
The driving clutch is used to couple and decouple the spindle and prime-mover (which can be a motor or gear-coupled shaft).
Basically, the prime-mover and spindle start out as disengaged but are engaged with the driving clutch when motion is needed.
Tool Post
Tool posts are essentially the tool holders — it’s where you put tools (particularly single-point cutting tools) in the turret lathe machine.
You can move the tool post horizontally, vertically, or even across the bed by using the carriage.
How Does a Turret Lathe Work?
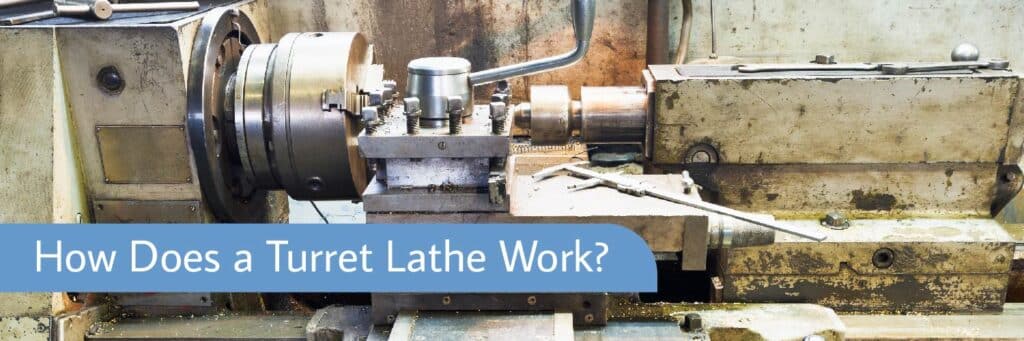
Below, I’ve listed down a general step-by-step on how a turret lathe works:
- Fix the workpiece in the power jaw chuck of the turret lathe and attach the tools you need to the hexagonal turret.
- You can rotate the chuck by rotating the spindle. This will also rotate the workpiece attached to the chuck.
- To adjust the distance of the hexagonal turret head from the rotating workpiece, just move the saddle. You can push the lever of a manual turret forward to do this.
- Rotate the indexable tool holder so the tool you need faces the workpiece. From here, two things can happen:
- When using a manual turret lathe, you (the operator) are the one controlling the lathe.
- Meanwhile, as the name implies, an automatic turret lathe has automatic turret indexing. This means that after every operation, the turret tool head will go back to the initial position.
Different Types of Turret Lathes
There are many ways to classify turret lathes:
- Size
- Method of control
- Bed orientation
- Number of turrets
But here, I’ll only talk about the more commonly-known types:
Horizontal Turret Lathe
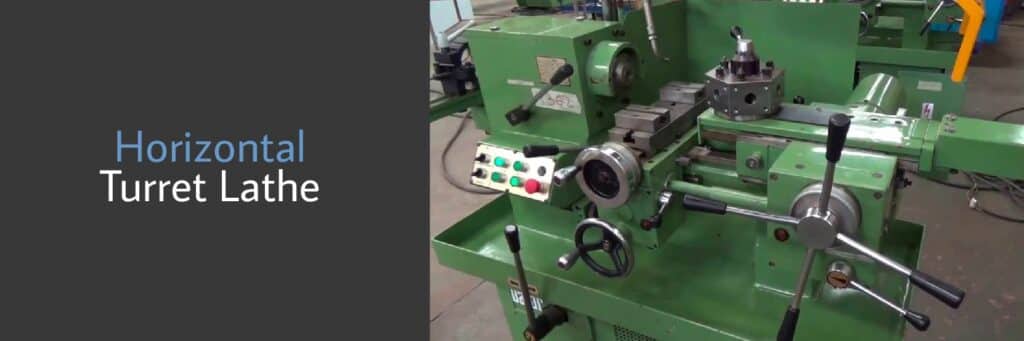
This is also called a manual turret lathe and is the oldest and most common kind of turret lathe.
As you can guess from the name, the turret is aligned horizontally from the workpiece.
Vertical Turret Lathe
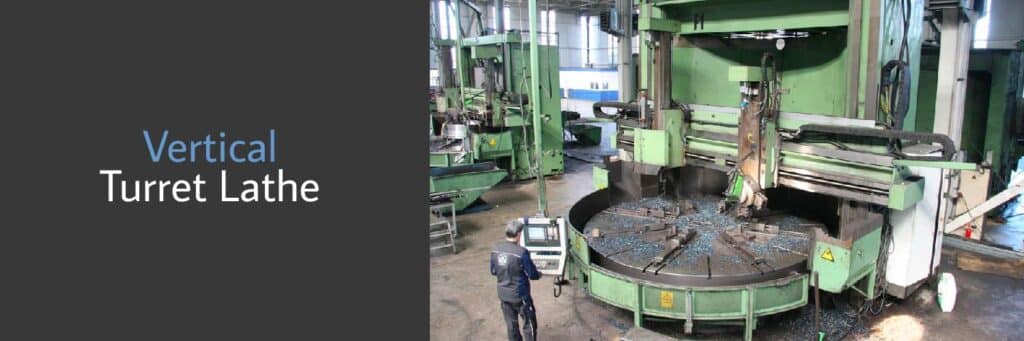
With vertical lathes (also called vertical boring mills), the workpiece is held VERTICALLY. You can think of the vertical turret lathe as similar to a huge potter’s wheel because of its horizontal rotating table.
A vertical boring mill equipped with a turret is good for large and heavy but short workpieces.
Aside from being able to move sideways, the turret can also be moved up and down. Additionally, a vertical turret lathe can actually hold 14 different tools.
Automatic Turret Lathe
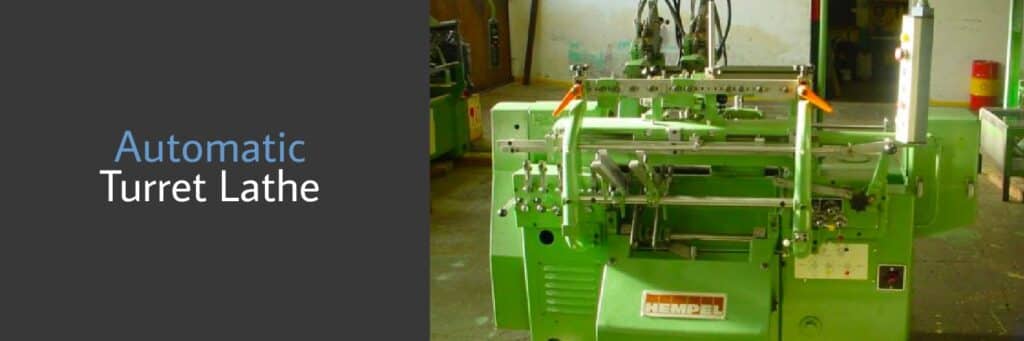
Automatic turret lathes are modifications of manual lathes.
These mechanically automated machines are ideal for mass production since they improve productivity by reducing machining time.
Automatic turret lathes are known by many names:
- For small- to medium-sized lathes:
- Automatic screw machines
- Screw machines
- For larger lathes:
- Chuckers
- Automatic chucking lathes
- Automatic chuckers
Computer Numerical Control (CNC) Turret Lathe
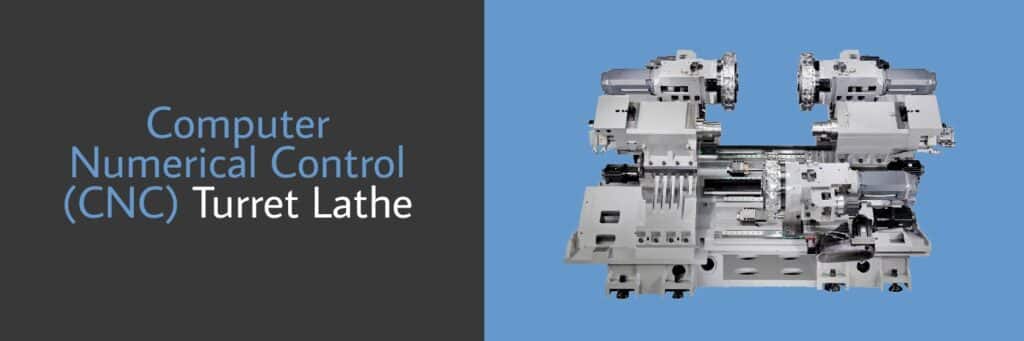
Computer numerical control or CNC turret lathes use computer programs to control different machine parameters — such as feed rate, spindle speed, and turret motion.
This computer system creates G-codes based on digital design.
Frequently Asked Questions
A turret lathe is similar to other lathes. To help you understand turret lathes more, I’ve answered a few questions below:
What Is the Difference Between a Turret Lathe and a Regular Lathe?
A conventional lathe can hold only a SINGLE cutting tool at a time. This can drastically reduce productivity since you’ll need to perform set-up tasks.
A turret lathe is an improved version of conventional lathes. The ability to station multiple tools around the turret tool head greatly improves productivity since you can do multiple operations in just one session.
What Is the Difference Between a Turret Lathe and an Engine Lathe?
The first difference you’ll notice is that an engine lathe can only house four cutting tools, meaning it initially takes less time to set up.
However, an engine lathe is slower to operate, making it unideal for mass production.
Engine lathes also require extremely skilled workers to operate. Otherwise, they can also use numerically-controlled turrets to let operators enjoy an automated selection of such machine tools.
Meanwhile, a turret lathe doesn’t have very strict requirements in terms of skill because of the existence of fully or semi-automatic turret lathes.
An engine lathe is also more expensive and larger.
It’s also more common to encounter tool wear problems with an engine lathe.
What Is the Difference Between a Turret Lathe and a Capstan Lathe?
The capstan and turret lathe have a lot in common. In fact, some people use “capstan lathe” and “turret lathe” interchangeably.
However, capstan lathes differ from turret lathes by quite a lot.
For one, capstan lathes can also have a hexagonal, square, or round turret. A capstan lathe is also more lightweight and faster.
However, compared to a turret lathe, a capstan lathe can only work on smaller workpieces — approximately half the size of the workpieces a turret lathe will handle.
A capstan lathe isn’t as rigid, either.
That’s because the turret lathe’s tool head itself is already mounted over the saddle as one unit. But with capstan lathes, the turret tool head is first mounted over the ram BEFORE being mounted over the saddle.
For a full summary of the difference between capstan lathe and turret lathe follow this link to another of our articles.
What Motor Is Used for Turret Lathe?
A turret lathe uses a stepper or servo motor.
This kind of motor has impressively high precision in RPM and angle of rotation — which are both VITAL in accurately working on the workpiece.
Are There Other Variations of Turret Lathes?
Yes, there are several variations:
- Monitor lathe – The monitor lathe’s turret resembled monitor-class warships. They’re essentially small- to medium-sized MANUAL turret lathes used for smaller workpieces.
- Flat turret lathe – Flat turret lathes are a kind of horizontal turret lathe. Here, the turret is flat, and the machine has overall better rigidity.
- Hollow-hexagon turret lathe – As the name implies, the hexagonal turret head is hollow. The main idea here is to improve the machine’s rigidity by letting a long part of the turret turn without the tool overhang.
- Toolpost and tailstock turrets – Yes, you can put turrets on non-turret lathes — such as engine lathes, toolroom lathes, and bench lathes.
Final Thoughts
Earlier lathes greatly improved thanks to the addition of the turret.
There are different kinds of turret lathes — from the vertical turret lathe to the CNC lathe. However, the oldest and most common is the horizontal lathe.
The turret head allows for multiple cutting operations, each with a different cutting tool, in quick and easy succession. This enables the machine to improve the manufacturing process time of metal goods.