Disclaimer: As an Amazon affiliate, I may earn a small percentage from qualifying purchases. This is at no extra cost to you. Learn more here.
Is backlash giving you headaches when you use your milling machine? Are you unsure what backlash means or how relevant it is to your machining?
In this quick and simple guide, I’ll be explaining backlash, backlash compensation, and how you can improve the efficiency of your milling machine tools.
What is Backlash in Milling Machining?
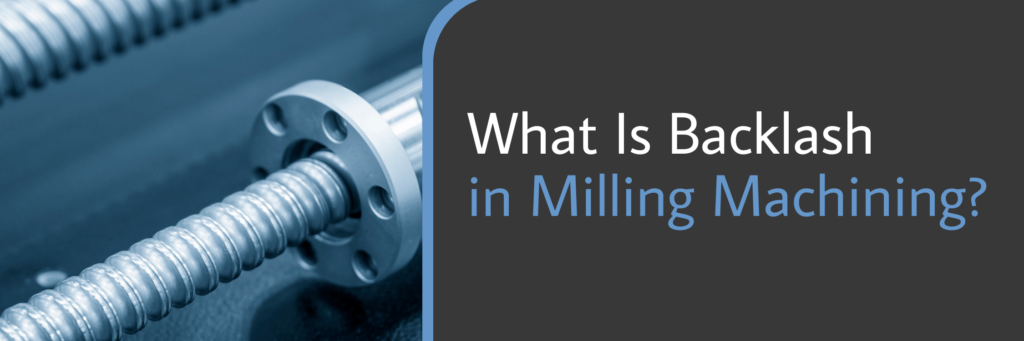
The term “backlash” refers to any non-movement that occurs during axis reversals due to gaps in the teeth or gears in machining tools.
For example, a machine is commanded to move 1 inch in a positive direction. Right after this, the same machine is commanded to have x movement 1 inch in the negative direction.
If the movement to the negative direction of the x motion isn’t immediate in the axis reversal, that means there’s mechanical backlash.
It’s important to eliminate backlash that’s excessive because you won’t be able to measure any machining holes in your x or y-axis properly.
This is because even if you move the machine one way or another (when the axis reverses direction), you’re not sure if the actual positioning accuracy of the machine is correct.
Signs of Backlash
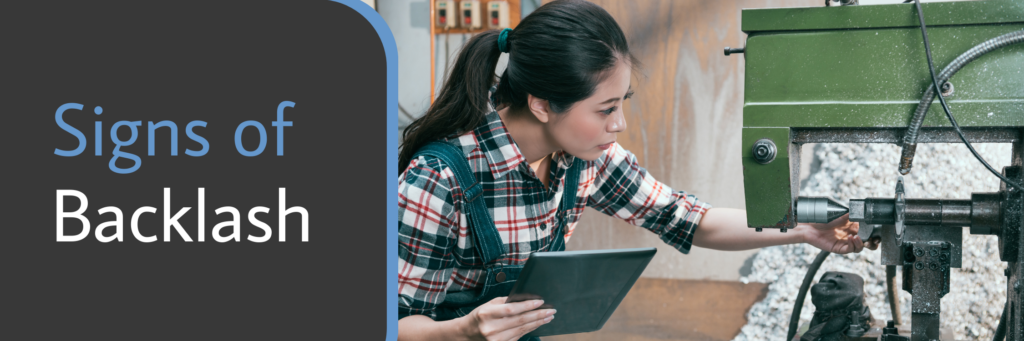
There are a few things you can check to determine whether machine backlash exists. The first is when milling circles using your machine tool.
If there is backlash present, a nasty witness mark will appear on each quadrant line in each axis direction (positive x-axis, negative x-axis, positive y-axis, negative y-axis).
Backlash is caused by normal usage, meaning that using a dial indicator is a standard procedure when performing your preventive maintenance program.
Normally, milling and CNC machine tools have low friction, but if you suddenly feel like it’s excessive, especially during axis reversals, then you should check for backlash.
I’ll discuss more about how to check for backlash in the ways to prevent backlash, measure backlash, and do backlash compensation sections below.
How to Prevent Backlash: 4 Compensation Methods
I’ll show you a few ways to perform a feature called “backlash compensation,” with options for both hardware and software backlash compensation.
Choose one that fits the equipment you currently have and that fits the tolerances you need when working on your milling machine.
1) Software Backlash Compensation
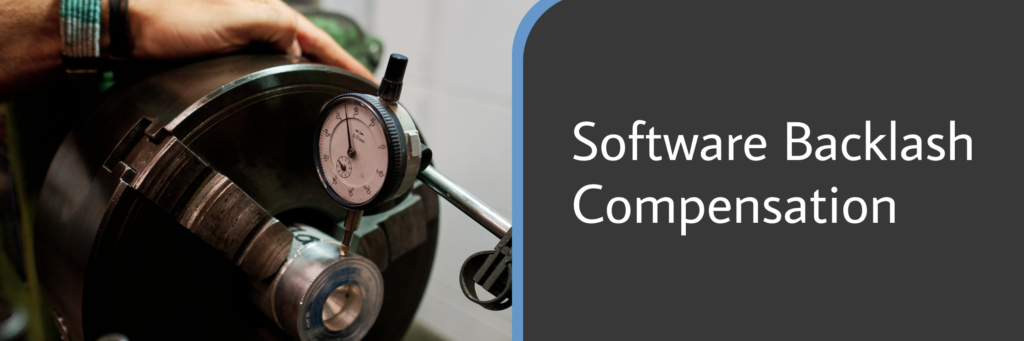
There are a few steps involved when troubleshooting backlash where a machine or tool electronically compensates for the backlash.
Using Dial Indicators
The first thing to find out is how much backlash you have. To do this, you need to use a dial indicator. The dial indicator will be placed on the individual gear teeth of the lead screw.
Then, you will simply move the lead screw a small amount. The difference between the number indicated on the dial connected to the lead screw versus the dial indicator is the amount of backlash you have.
Using the Electronic Control System
The software works only if you input the amount of backlash into the machine. The computer control knows how to integrate the backlash amount to the amount the machine will move.
The software will simply add or remove the extra y-axis movement or x-axis movement backlash, depending on what you’ve measured, to keep your process running smoothly.
This will reduce the backlash that your nut threads induce. This helps minimize errors, especially when you need critical holes machined.
In turn, it improves positioning accuracy by ensuring hole locations are exactly where they’re supposed to be.
2) Preloading or Anti-Backlash
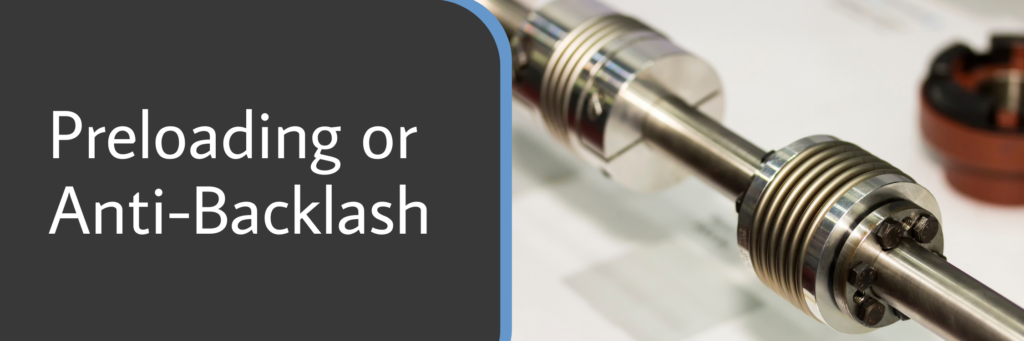
The anti-backlash nut is a split nut that pulls the screw from either side. Whether it goes in the same direction, positive direction, or negative side, any slack is minimized.
This is because the two nuts will take up or impose a load on both sides of the screw even if it’s not traveling in that direction.
The y motions and x distance won’t be affected by the existing backlash because the two-sided anti-backlash nut is always keeping the screw preloaded.
This is true for both positive and negative x-direction or x distance and positive and negative y direction or y distance.
3) Single Direction Positioning Mode (Using the Same Direction)
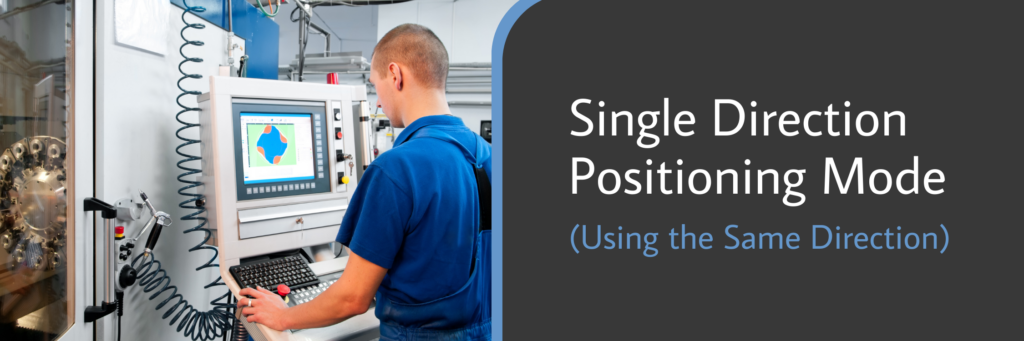
Another way to compensate is to approach motion in the same direction each time when using CNC machines where backlash exists.
Single-direction positioning means that the positioning movements will always go in one direction so that you never trigger a situation where backlash affects the machining.
For example, in machine holes using your CNC machine, the boring bar moves in the same x-axis and y-axis each time. This can be adjusted in software like Fanuc controls.
However, while this may work with boring bars, it might not work when using a large horizontal machining center.
Due to the large weight of the headstock, it would always be wise to use the negative y-direction unless properly counterbalanced.
The controls use the single-direction positioning mode so that you don’t have to manually program the appropriate approach motion using simple motion commands.
In this case, the control machine will first move the boring bar in the x or y-axis with the backlash and then move it with the programmed coordinates.
4) Adjusting the Machining Centers
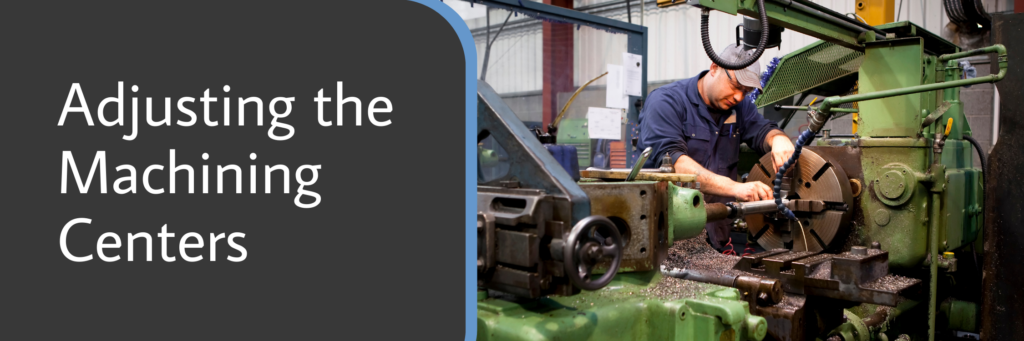
This method is usually done when compensating for backlash through other methods isn’t enough.
It’s also done when absolute precision is needed in your milling machine, like when using a boring bar to drill precise holes, where any positioning errors are a big deal.
The simplest method involves replacing the whole part that has too much backlash. This is a great option if the part has worn out or wasn’t constructed with the best quality.
Another method is to take it into a professional machining shop and have the backlash properly adjusted depending on what you’ve measured.
This is the ideal solution for things like box-way construction.
It helps to reduce excessive vibrations when performing powerful machining operations when backlash exists and the axis drive systems are not rigid.
Hardware vs. Software Backlash Solutions
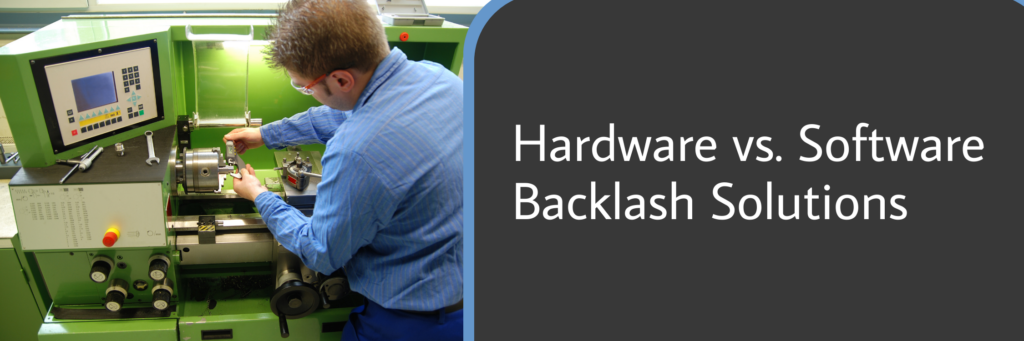
Solving for backlash can be done in two ways – through the actual practice of adjusting or adding hardware or using software backlash compensation.
I’ll talk about the advantages and disadvantages of using either type of method for backlash compensation.
Hardware Compensation
Using things like a preloading nut or replacing the machining centers is great because the y or x-axis experiences actual hardware correction.
This means you don’t have to keep the backlash amount that exists in mind and have to compensate for it each time you use your CNC machine. You just need to have the fix “one and done.”
However, hardware compensation can be tricky because the right preloading nut or replacement can be expensive or hard to find.
Software Compensation
On the software compensation side, it’s great if you have multiple machines that have backlash because you can switch the control machine between each of them.
It also doesn’t interfere with any hardware, meaning that there’s less of a chance that a hardware part you’re adding or replacing will mess up your projects.
For example, you might accidentally get the wrong size ball screws or preloading nuts and unintentionally damage either your CNC machine or the piece you’re working on.
However, software compensation can be expensive upfront. Depending on the control machine you want, it may be out of your budget.
How Bad Can Backlash Get?
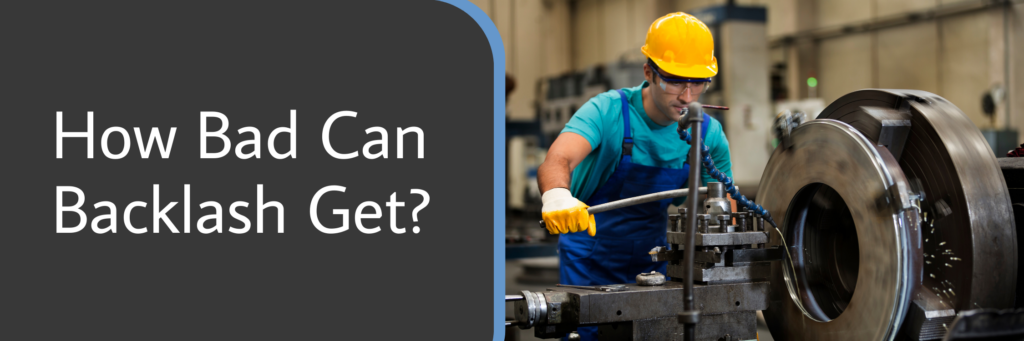
Backlash can get to the point where excessive vibration, heat, and movements will cause damage to the parts inside the milling/ CNC machine or on the piece you’re working on.
The motion departure can also be wildly different than the motion you wanted the machine to move, meaning you’ll have inaccurate work.
The parts of the tools can also begin to wear faster, fall off, or not function properly.
For example, the nut holding the end of a machining center might fall off easily compared to when it was new because the machining screw has too much slack.
In any case, it’s an issue that can grow over time. I recommend adjusting for it or having a hardware fix for it as soon as you find out it exists.
Frequently Asked Questions
Now that you know more about how backlash works and methods on how to fix it, you might have some questions related to the different types or how to determine if there are any.
I’ve answered the most commonly asked questions below.
How Do You Determine Backlash?
The best way to figure out how much there is in your milling/CNC machine is to use a dial indicator to measure the total amount.
This is done by attaching it to the CNC machine screw teeth or threads and rotating it a certain amount to one side.
The difference between the rotated amount and the amount on the dial is the backlash amount that you have.
What Are the Different Types of Backlash?
There are four types that are usually seen in gear or screw designs:
- Circular
- Normal
- Center
- Angular
Some types are more prevalent in things like car differentials, whereas others are more seen in milling machining.
What is Backlash Clearance?
Clearance is just an alternative way of saying the term. It’s called clearance because there’s an extra space between the teeth of the screws and the threads.
Conclusion
Backlash is a common problem that happens in milling machining, and it shouldn’t alarm you too much if you encounter it.
However, it is something you should compensate for immediately if you want to keep your projects accurate and of high quality.
Use a combination of both hardware and software methods to get the best results. Hopefully, this article has helped you alleviate some of the issues you have.