Disclaimer: As an Amazon affiliate, I may earn a small percentage from qualifying purchases. This is at no extra cost to you. Learn more here.
What is a lathe machine?
Lathe machines are an integral part of any machining operation for those in the know and a highly confusing machine tool for those who aren’t.
However, to say they’re quite useful is an understatement.
A lathe is an exceptional machine that can do many things if you understand how to use it and what it’s used for.
It’s extremely versatile and has countless small and large-scale industrial uses.
Let me take you through what a lathe is, its parts, uses, and everything you need to know about it.
Key Takeaways:
- A lathe machine is the “mother of machining.” It spins your workpiece and slices it to your desired shape with a stationary cutting tool. It’s an important part of the machining process.
- A lathe comprises a headstock, tailstock, bed, carriage, feed rod, lead screw, handwheel, and chip pan. All other parts are located inside these main portions.
- You can operate a lathe machine by loading and securing your part, choosing your tools, calibrating your settings manually or via computer, and activating the machine.
- There are three main types of lathe machines: an engine lathe, a turret lathe, and a special lathe.
- You can use a lathe machine for woodworking, glassworking, thermal spraying, metalworking, and ultra-precision cutting. It’s great for manufacturing and artistic work!
What Is a Lathe Used For?
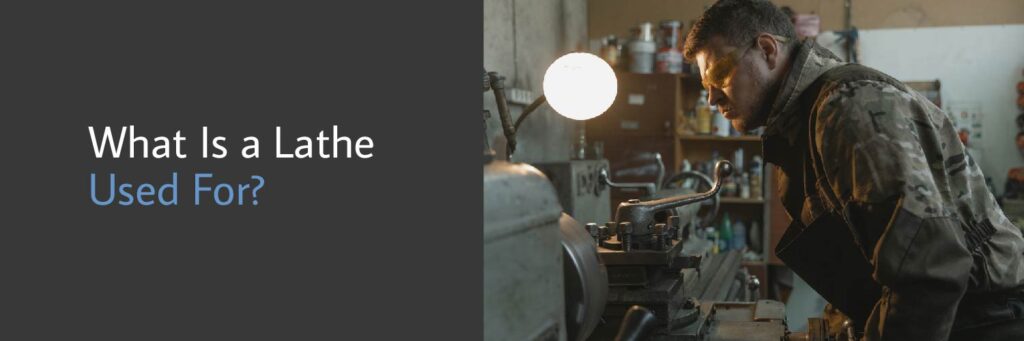
A lathe is a machine that places metal, wooden, or even glass pieces on an axis of rotation, then applies precision cutting to get a nicely-shaped workpiece that can be used for industrial or artistic purposes.
While suitably-equipped metalworking lathes are similar to a milling machine in function and design, the main difference is that the object spins.
At the same time, the tools stay stationary on a lathe. The opposite is true on a milling machine.
Lathes are used for metal spinning, thermal spraying, knurling, drilling, facing, cutting, grinding, and creating symmetrical shapes.
You can make EVERYTHING with lathes, including car parts, gun barrels, sporting equipment, crankshafts, table legs, vases, rolling pins, and wedding rings.
They’re even heavily used in aeronautics!
With enough technical knowledge and professional experience, you’d be surprised what you can create and manufacture with a lathe, especially CNC lathes that you can program via computer.
When Was the Lathe Invented?
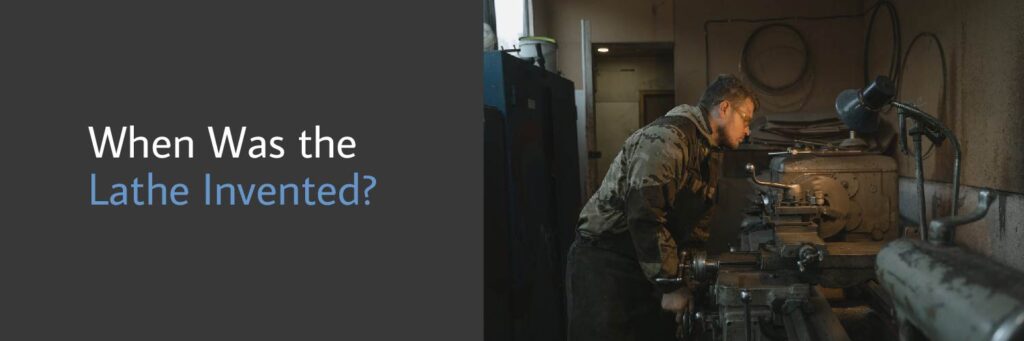
The lathe machine is often considered the “mother of machining” because it was possibly the FIRST machine tool ever made. Its origins can be traced back to ancient Egypt.
Lathe operation was highly similar to a pottery wheel, except it had a spinning rotating workpiece that workers could shape and cut with early machine tools instead of just using their bare hands.
These ancient lathes were free-hand, with workers maneuvering around the length of the workpiece. As technology progressed, lathe operation became more precise and consistent.
Modern lathes first saw heavy use in 1569 in France for woodworking purposes.
However, the Industrial Revolution led to the popularity of the metalworking lathe and the invention of engine lathes.
This type of lathe machine made the machining operation even smoother and more precise.
High-speed lathes with enough torque to rotate heavy parts were combined with an automatically-controlled cutting process.
CNC lathe machines that operated via computers soon followed, turning the lathe into one of the most used machine tools in any modern-day workshop.
It continues to grow more versatile as time goes on!
What Are the Parts of a Lathe Machine?
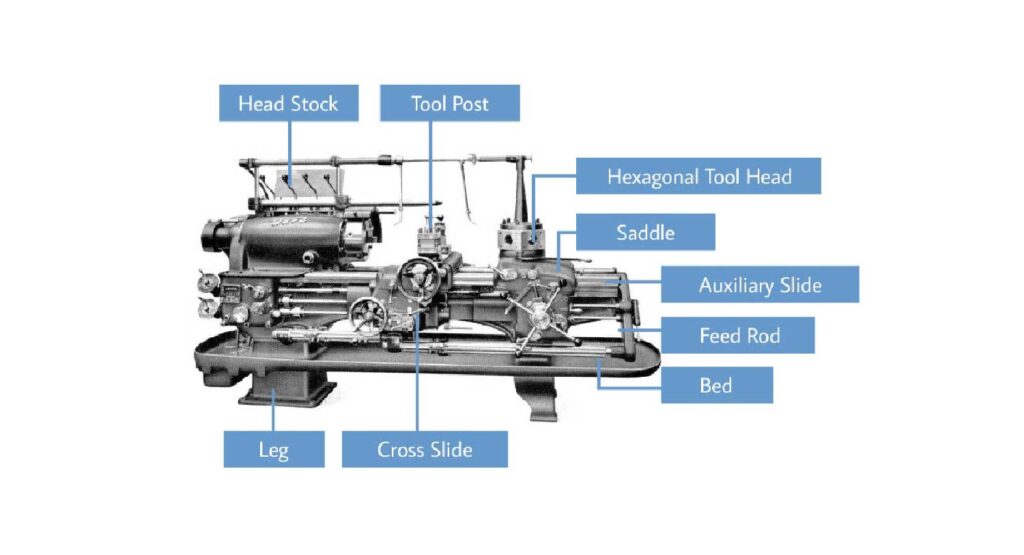
An engine lathe consists of several different parts that allow it to work the way it should. Here are all the components every machine shop lathe machine should have:
Lathe Bed
The lathe bed houses all other parts of the lathe. The length of your bed determines and limits the length of the workpiece.
Headstock
Your headstock houses all the components related to spinning the workpiece, such as the spindle, controls, and chuck.
Tailstock
This piece allows you to work on longer workpieces. It’s mounted on the right of the lath and moves along the Z-axis.
Main Spindle
The spindles are the part that creates your rotating workpiece. Spinning your material allows you to work on the shape, size, and length.
Motor
High-speed lathes like the engine lathe are only called such because they are classified as machine tools.
This is thanks to their high-powered motors, which generate spindle speed and even tool movement.
Chuck
The chuck holds the workpiece in place, and it’s mounted on the spindle. It ensures proper alignment and the best cuts possible.
Carriage
This portion is responsible for positioning, guiding, and mounting the cutting tool and all the corresponding controls.
Saddle
This carriage part is H-shaped and supports the tool post and compound rest.
Cross Slide
The cross slide allows you to mount your tool post or any cooling equipment. It allows you to slide your tool to and fro.
Compound Rest
This part sits on top of the cross slide and supports your cutting tool in any position you need it in.
Tool Post
The tool post allows you to mount your tool holder.
It allows you to choose the right tools from your tool holder and switch tools out relatively quickly.
Apron
The apron is clamped to the saddle to hold the gears that interact with the cross slide. It is another component that guides the tool bit where it needs to go.
Feed Rod
The feed rod allows you to maintain the right linear movement you want your tool to take.
Lead Screw
The lead screw moves the whole carriage while traversing the compound slide. The lead screw is essential for ensuring the efficiency and stability of your cuts.
Cutting Tools
Your cutting tool is used to shape, cut, and form your workpiece the way you need it to be. It allows you to turn it from a cylinder to any unique shape you need.
Lathe tools, like the rough turning tool, are supposed to be cutting-edge.
How to Use a Lathe Machine
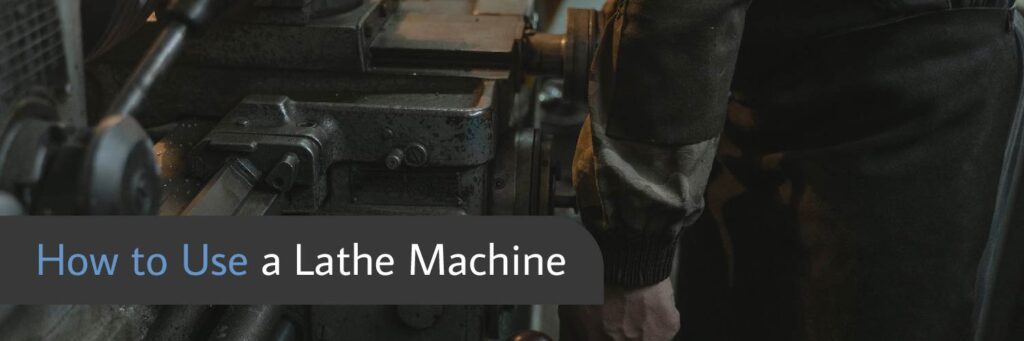
An engine lathe is a precision machine tool that can slice your fingers off if you aren’t careful.
That’s why you need to understand how it works and what you need to do to calibrate it correctly.
While it may take years of instruction and experience to operate a lathe machine, here are the steps you can take to get your workpiece processed into your desired shape.
Step 1: Power the Machine Tool Down
Lathe machining is so effective because it employs sharp tools and fast rotation speeds, both of which can cause injuries and lost fingers or flying debris if you aren’t careful.
This is why you must ensure your machine is turned OFF until you’re ready to work and paying complete attention.
This step is for your SAFETY and the LONGEVITY of your machine.
Step 2: Mount Your Workpiece
Once ready to work, you can place your workpiece between the headstock and tailstock and buckle it down with the chuck.
Make sure it’s secure and installed correctly!
Once mounted to your machine tool, your workpiece rotates with the help of a spindle.
The spindle rotates your machine along the axis as it’s connected to the motor.
Step 3: Install Your Cutting Tool
Your workpiece would just be an extremely fast cylinder if you didn’t have a cutting tool to work your material into your desired shape.
You will thus need to install your stationary cutting tool.
Make sure it is secure and firmly in place, as it shouldn’t fly off during your process.
If you’re working manually, you must place your tools on your pre-marked spots once your machine starts spinning.
Step 4: Calibrate Your Settings
If you are using an automatic or CNC lathe, you will now need to input your calibrations or specific designs to get the most PRECISE and accurate cuts, grooves, and shapes possible.
Using a CNC lathe machine allows you to input your CAD design and leave your machine to do its magic once it’s activated.
That said, lathes work quickly, and it’s better to keep an eye on them throughout.
This step entails double-checking your mounting and rotation speed if you’re working with a manual lathe.
Choosing the right tools beforehand saves power and any potential headaches down the line!
Step 5: Activate Your Lathe
If you think about it, the lathe is a simple machine.
It has a mechanism to spin the material and a place to mount it, and any tools you will need to work it.
Once everything is set to your preferred specifications, you can activate your motors and spin your object.
CNC workers can then monitor and observe as the machine moves the workpiece around the tools.
Manual workers can also use their skills to handcraft their workpieces, relying on speed and momentum to get consistent shapes on both sides of their workpieces.
Types of Lathe Machines
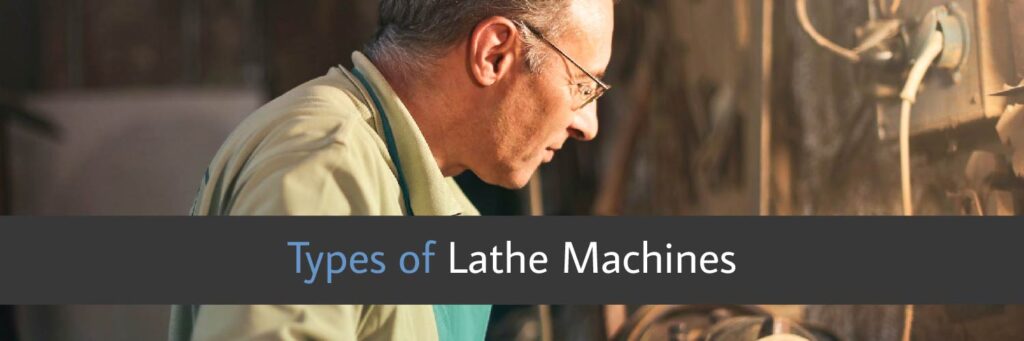
Now that we’ve answered the question, “What is a lathe?” it’s time to look at the many different types of lathes.
I will discuss each lathe machine type, their maximum length and speed, and the things that set them apart.
Engine Lathes
An engine lathe machine, also known as a center lathe, can move the cutting tool vertically and horizontally.
An engine lathe or center lathe is primarily used to cut and form metal.
Engine lathes are often CNC nowadays, allowing for precise, mass-produced movements and cuts.
Speed Lathes
As the name implies, speed lathes move incredibly fast. They’re used for cutting small details and finishing rough cuts.
Turret Lathes
A turret lathe is designed for manufacturing and mass-producing duplicate parts.
Its turret allows you to easily spin the workpiece across different tools without replacing or recalibrating tools.
Tool Room Lathe Machines
A toolroom lathe is a center lathe that is maximized for workroom labor. The toolroom lathe has all the professional bells and whistles you’d want in an engine lathe.
Glass Lathe Machine
A glass lathe machine is specifically designed for glass working.
It allows workers to mold and shape this volatile material while it has not yet solidified. It does not rely on cutting tools.
CNC Lathe Machine
CNC machines, such as a CNC lathe machine, rely on Computer Numerical Control. This type of lathe is programmable and codable.
It allows you to get the most precise cuts with minimum human involvement.
Vertical Turret Lathe
Unlike other horizontal lathes in design and mounting, vertical turret lathes hold the workpiece vertically with the headstock on the floor.
You get more maneuverability and flexibility with this type.
Hollow Spindle Lathe
This lathe type contains a hollow spindle, which allows you to cut and drill more efficiently.
Gap Bed Lathe
This type of lathe has a gap in the bed between the headstock and tailstock.
This allows you to work with longer or larger pieces by creating a buffer between the mounting stocks.
Capstan Lathe
The capstan lathe is centered around a vertical spindle or capstan, which holds and rotates your workpiece during machining.
It is primarily used for complex mass production.
It’s sometimes confused with a turret lathe, if you want to know why, look at our article about the difference between capstan lathe and turret lathe.
Bench Lathe Machine
A bench lathe is specifically designed to work on a workbench surface. It’s for small-scale and amateur operations.
It’s perfect for those looking to practice lathe work in their spare time.
Special Purpose Lathe Machine
Several other lathes serve specific purposes, such as vertical lathes, ornamental lathes, and multi-axis lathes.
It is configured to meet specific demands, shapes, or work patterns.
Automatic Lathe Machine
Automatic lathes can be programmed and made to work automatically and autonomously. CNC lathes fall under this category.
Types of Lathe Operations in Machining
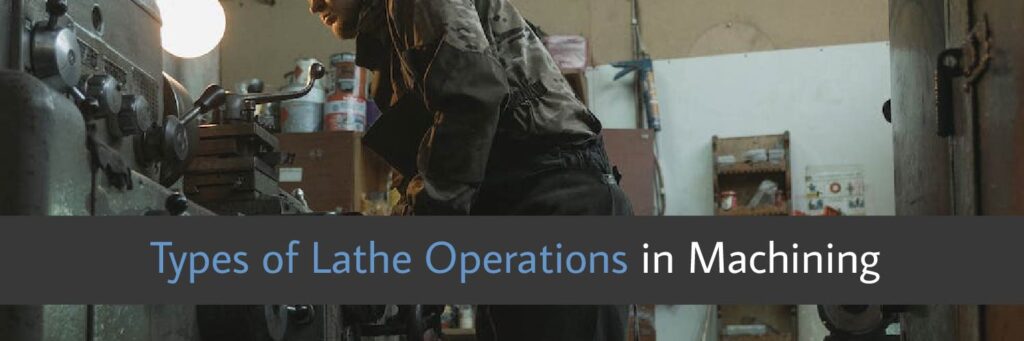
Having looked at the types of lathe machines, let’s look at some common lathe operations that overlap or make it unique from other machine tools.
After all, you’d be surprised what the lathe in your machine shop can do when you use the right stationary cutting tool!
Turning
This is the most common operation out of all the processes that require lathe machining tools.
It entails using a turning tool to whittle down your piece to your desired dimensions.
Depending on your turning tool, you can have a rough go that removes as much material as possible or a finish that smooths out the final product.
Taper Turning
Taper turning is a subset of turning that utilizes an incline movement between the cutting tool and your workpiece to smoothen the transition between varying diameters.
Taper turning allows you to make smoother, more elegant shapes like chess pieces.
Facing
This step reduces any excess material to get your piece to be the right total length.
Cutting Tool
Your lathe is in your machine shop because it’s one of the best cutting tools out there.
You can install compatible cutting tools into your machine to get the desired effect, shape, and size.
Grooving
Using a grooving tool allows you to create a narrow indent or groove in your piece. It can be divided into face and external grooving.
Knurling
A knurling tool creates a form of scoring and texturing on the surface of the workpiece. Your knurling tool creates serrations that raise and lower certain areas of your piece.
Boring
This allows a lathe to penetrate the workpiece and create a medium to large hole or tunnel on the inner diameter of the piece.
Threading
Using a thread-cutting tool allows you to move alongside a workpiece to create spiral grooves or threads on the outer layer of your workpiece.
This is how bolts and screws are made.
Drilling
Using drilling machine tools allows you to tunnel through the interior of your workpiece, removing material and creating a hole the size of your drill bit.
Metal Lathes vs. Wood Lathes
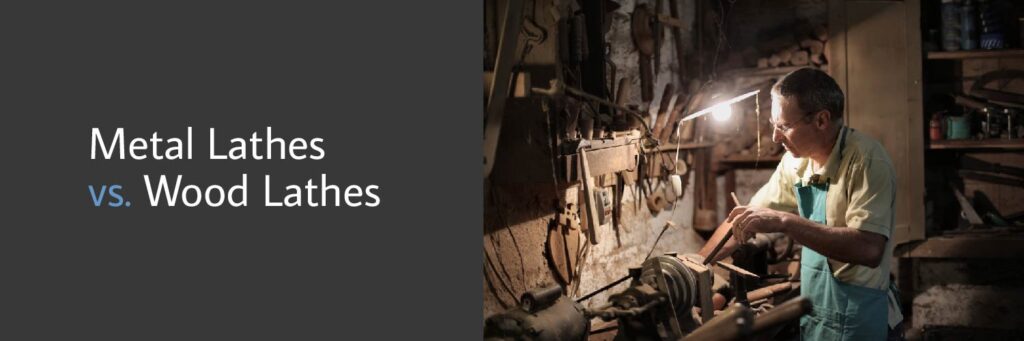
Metalworking lathes are particularly designed for metal spinning, cutting, and shaping metals like aluminum, titanium, and steel.
Such lathes are specifically designed to cut through metals, and a wood lathe can’t.
Here are some of the machining tool specifications that make metal lathes and wooden lathes different:
Engine Power
Metal lathes are often larger in size and scale, requiring more powerful engines and motors.
Wood lathes are often smaller in terms of operation and need less engine power, as wood is easier to cut through.
Rotation Speed
A metal lathe moves incredibly fast to possess the torque needed to spin heavy metal workpieces, and the speeds are adjustable for accuracy.
Wooden lathes, meanwhile, run between 500-1200 rotations per minute.
Size of Cutting Tools
Metal lathes deal with industrial quantities of metal that can be used for large vehicles like airplanes and submarines.
This necessitates using larger tools that need to be mounted on the machine.
Wooden lathes do not need to have tools as big because they’re used for more artisan purposes. Woodworkers will often use hand tools to get their desired shape.
The Sharpness of Cutting Tool
Wooden lathes do not need tools to be overly sharp, as the spinning motion makes existing hand tools that much more effective.
A metal lathe needs to be extremely sharp not to get any jagged edges or imprecise cuts.
After all, pieces made on a metal lathe need to be of extremely high quality, meaning they must be precisely formed, which is why some lathes even employ waterjet cutting.
Applications of a Lathe Machines
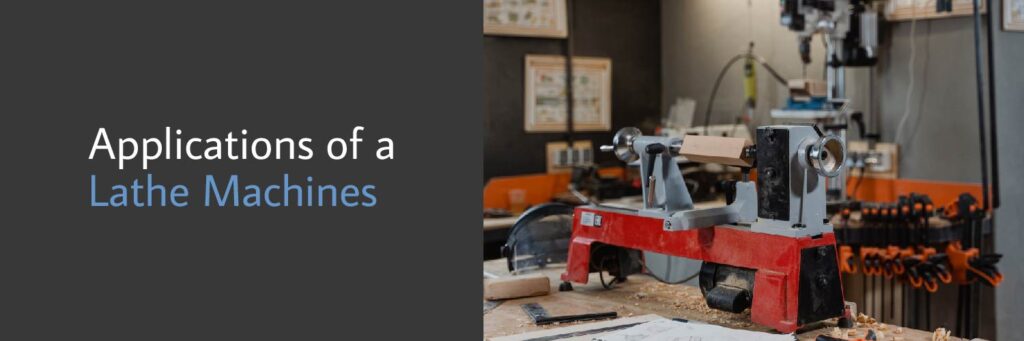
A lathe machine has plenty of uses, whether it’s for large-scale manufacturing or delicate, dedicated artistic work.
Let’s look at some settings where a lathe will most come in handy:
Industrial Applications of a Lathe Machine
As a machining tool, a metal lathe is essential for metal spinning, shaping, cutting, resizing, filing, and processing, which is what allows it to be used in large-scale vehicle manufacturing.
Lathes are useful because they can perform the following tasks depending on which tool is installed:
- Sanding
- Shaping
- Drilling
- Knurling
- Turning
- Deforming and
- Cutting
You can use a lathe to build nuts, bolts, assorted car gears and parts, airplanes, submarines, firearms, high-grade medical equipment, and more, depending on your equipment size.
Small-Scale Applications
Smaller-sized or mini lathes are also useful for watchmaking, making sporting equipment like baseball bats, pencils, hammers, or woodworking.
Amateurs or smaller-scale operations can also use manual and CNC lathes to produce fine details like those needed in watchmaking and even chess sets.
In this case, you’re limited only by your creativity and competence when working with a lathe.
As long as you have a bit of wood or workable metal, you should be able to create amazing things!
Frequently Asked Questions
You can’t ask too many questions when it comes to operating lathes.
Lathe machine operation requires an eye for detail as this machine tool is designed for precise, high-speed movements.
Allow me to answer some of the most common questions potential lathe users have when using a lathe machine:
What Are the 3 Types of Lathes?
While I covered over a dozen different lathes in the list above, these lathes can be divided into three main types: engine lathes, turret lathes, and special lathes:
- Engine lathes are horizontal lathes primarily designed to cut through metal parts. It is often used to spin sheet metal and is heavily used in industrial manufacturing.
- A turret lathe is also a type of metalworking lathe that can be either vertical or horizontal. It cuts interchangeable duplicate parts and resembles a swiveling gun turret, hence the name.
- Lastly, special lathes possess specific purposes and can be used for artisanal and smaller-scale shop work. Bench-type jewelers’ lathes and crankshaft lathes that look like they belong in a car engine fall under this category.
What Are a CNC and Lathe?
A CNC lathe is a lathe machine that falls under computer numerical control.
This allows the cutting process to be entirely automated and therefore repeated for the mass production of parts.
The movements on CNC lathes are programmed with CAD 3D design software and coded in G-code, which allows for the most precise and detailed cuts and shapes possible in the shortest amount of time.
This allows for the highest possible levels of productivity and output without putting factory workers in the risky, debris-filled factories of the early 20th century. Welcome to the future!
How Do I Become a Lathe Operator?
A manual lathe operator will need a high school diploma or a GED as a minimum educational requirement.
You can then enroll in a vocational or community college course on machining.
You can also choose to apprentice with a lathe machinist for 2-3 years to learn the ropes, which will allow you to receive the certification to go solo and operate a lathe independently.
While modern CNC machining may require a knowledge of programming or 3D modeling, many of the skills, especially those used on conventional lathes, can be taught as long as you’re eager to learn and are driven.
Conclusion
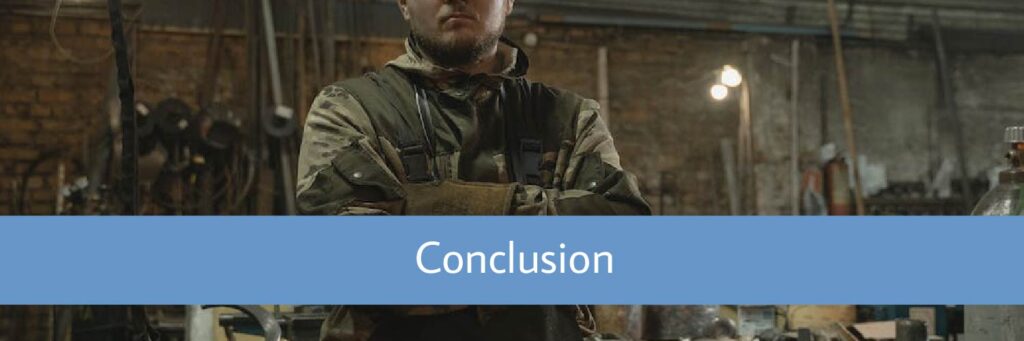
A lathe is a machine that shapes wood and metal by spinning it, allowing it to be cut and formed with ease.
This, plus precision CNC control, has made the lathe machine an indispensable part of the machining process.
It’s a must-have in every machine shop and even small-scale artisan work.
Whether you plan on using a lathe for sculpting elegant wood furniture or machining spare car parts, you can rest assured knowing that your lathe machine can do it all with proper care and knowledge.