Disclaimer: As an Amazon affiliate, I may earn a small percentage from qualifying purchases. This is at no extra cost to you. Learn more here.
Last Updated on March 1, 2023 by Charles Wilson
The highest machining accuracy of milling equipment greatly influences the degree of refinement of the processed product.
Some are worried about the process’s accuracy, how to achieve precision, and how to lessen the impact of outside influences on precision machining performance.
This article will discuss the variables impacting the highest machining accuracy and suggest how to do so.
KEY TAKEAWAYS:
- Milling and cutting workpieces with spinning multi-edge machine tools is a very effective processing technique. It can be used in processing planes, various forming surfaces, and special shapes of molds.
- When creating a product, milling enables you to regulate the product’s particle size.
- Hard materials like steel can be machined with greater precision and accuracy than softer materials like aluminum.
Factors That Affect Milling Machine Accuracy
The factors that might affect the machining accuracy of a machine are listed below:
1. Precision of the Actual Machine Tool
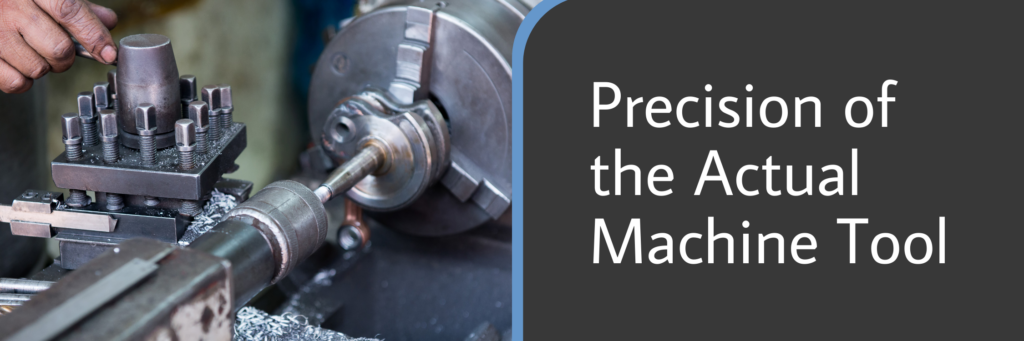
The variation in positioning accuracy will result in mistakes in the workpieces caused by the machine tool if the machining accuracy of the coordinate axis of the tool is not high.
The machine tool’s positioning precision has an impact on the spindle’s vibration frequency as well. The forming surfaces become rougher the higher the spindle vibration frequency.
A variety of tool coordination is necessary for the machine tool to operate.
NOTE: The turning tool executes cutting processing of linear or curved movement in the plane while the workpiece rotates. It is generally performed on a lathe to process the inner and outer cylindrical surfaces, conical surfaces, and end surfaces.
2. Choosing a Milling Cutter
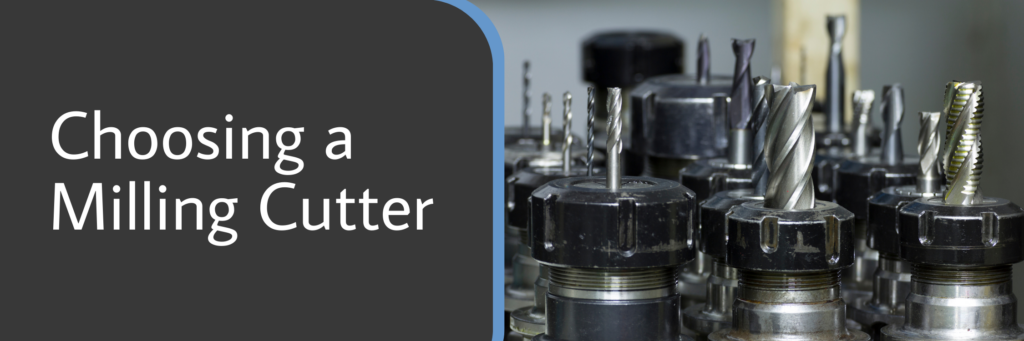
Other parameters, such as the milling cutter’s shape, the design of the structural components, and overall selection, will alter the milling cutter’s accuracy.
The surface roughness of milling is typically 6.3-1.6 m, and the accuracy ranges from IT8 to IT7.
- Surface roughness during rough milling is 5-20 m, and the machining precision is IT11-IT13.
- Surface roughness for semi-finishing milling is 2.5–10 m, and the accuracy ranges from IT8–IT11.
- The surface roughness of finishing milling is 0.63 to 5 m, and the accuracy is IT16–IT8.
NOTE: Rough turning strives to improve turning efficiency without lowering cutting speed by using a large cutting depth and large feed on a lathe, but the accuracy can only reach IT11, and the surface roughness is Rα20-10μm.
3. Use of Workpiece Clamping Improperly
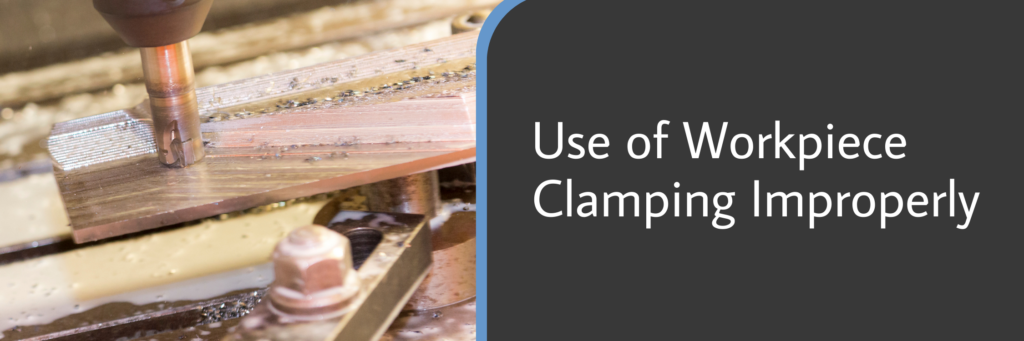
The worker fixes the thin workpiece in the fixture and moves on to the next phase using a machine to process it.
The thin workpiece may distort and lose machining accuracy if the clamping position is improperly planned and the force is improperly managed.
When using thin-cutting machine tools, care should be taken with the clamping position and the workpiece’s thin shaft.
NOTE: Milling is the term to cut workpieces with rotating, multi-edge tools. The two types of milling are down milling and up milling, depending on whether the workpiece feed direction and main movement speed are moving in the same or opposite direction.
How to Improve Milling Accuracy
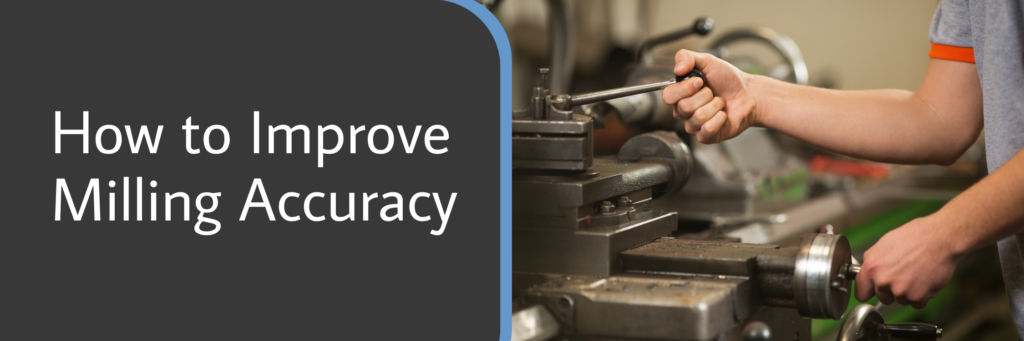
The ways how to improve the machining accuracy of milling are found below:
1. Control the Level of Vibration When Processing
In the course of milling, vibration frequently happens. The machining accuracy will be significantly impacted if the vibration frequency is too high.
Workers choose a highly efficient processing method to increase the production accuracy of workpieces with the following:
- Improve the overall stiffness of cutting tools and other parts
- Adjust the assembly coordination of various parts
- Make all links of work closely cooperate
- Reduce the potential vibration frequency
NOTE: When non-ferrous metal parts are turned at high speeds on high-precision lathes using finely honed diamond turning tools, the machining accuracy can approach IT7-IT5, and the surface roughness is R0.04-0.01m. Mirror turning is the name given to this type of turning.
2. Control the Machine Tool’s Entire System
The workpiece’s machining precision will depend on where the machine tool’s coordinate axis is positioned, and it will also depend on how accurately the tool’s surface is manufactured.
Before using the machine tool, it is important to:
- Monitor its components closely
- Check the coordinate axes’ location and workpiece surface roughness/quality
- Remove any reversible variables
- Enhance the machine tool’s overall performance
NOTE: Try to use a high speed, a small feed, and a shallow cutting depth while finishing and semi-finishing turning. The turning precision is generally IT8-IT7, and the surface roughness is 1.6-0.8μm. Planing normally has a surface roughness of Ra6.3-1.6 m and machining precision at IT9-IT7.
3. Choosing a Milling Cutter and Installing a Milling Cutter at an Angle
Before choosing a cutter, the staff must be aware of the following:
- Kind of milling cutter appropriate for the current operation
- Comprehend the milling cutter’s specifications
- Choose the milling cutter that is best for the entire system
4. Choosing a Workpiece Clamping Technique
It has been mentioned that the suitable degree and machining accuracy of clamping somewhat influence the workpiece’s total precision.
Different clamping techniques are needed for the creation of different workpieces.
Before learning to precisely set the clamping process on the machine tool, the crew must first comprehend how to match and clamp the workpiece.
Importance of Accuracy of the Machine Tool
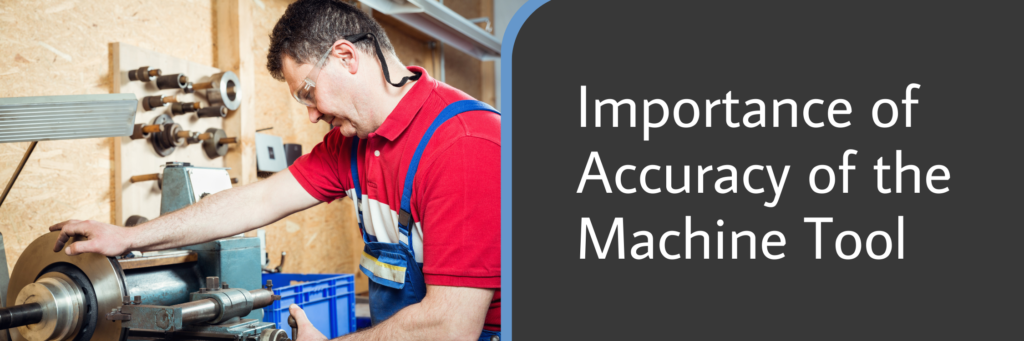
The machining accuracy of the machine tool greatly influences the degree of refinement of the product.
The turning precision will be higher if we operate both traditional and CNC machine tools at the same technological level. After all, some machines have greater control than people.
The control now has greater precision and high accuracy. Also, the machining accuracy will be reduced if the machine is old, machine parts may have issues, and the electrical system malfunctions.
What Is the Difference Between Accuracy and Precision?
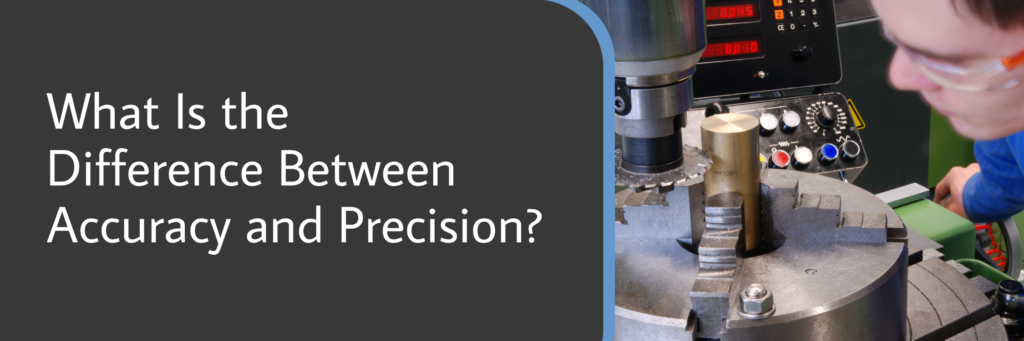
Accuracy is the degree to which your shot is about the center of the chart. Precision is the capability of a measurement system to return the same measure repeatedly.
The state of the CNC machine also impacts the end product’s precision and high accuracy.
A very accurate CNC machine service guarantees that the metal piece will be accurately and error-free cut to your specifications using CNC milling tools.
What Are Tolerances?
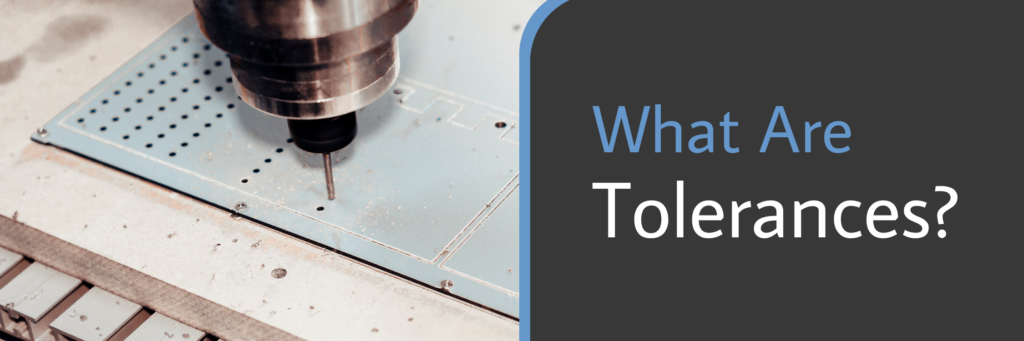
The degree of permitted variation in a part’s dimension is its tolerance.
Let’s use the example of a CNC machine shop that claims its machining tool can reach a tolerance of 0.05 mm to comprehend this better.
The difference from your standard value caused by their machining procedures could be up to 0.05 mm greater (or less).
If you ask them to drill a hole in a metal block with a diameter of 10 mm, you can expect to receive a hole from 9.95 mm to 10.05 mm.
Because tolerance is crucial, even a small error can impair your design’s function.
Frequently Asked Questions (FAQs)
The following are some of the most frequent queries about the precise milling machine:
How Accurate Are CNC Machines?
This is due to the following capabilities of CNC machining: A high level of part complexity. Tight tolerances, usually between 0.0002″ and 0.0005″ (0.0127 to 0.00508 millimeters).
Nowadays, most manufacturers are using accurate CNC machine tools.
What Tolerances Are Normal for CNC Machining?
For a CNC machining service, the usual tolerance is 0.005″. The machining tolerances can be as close to 0.001″ or around the width of a human hair.
What Are the Advantages of High-Speed Precision Turning?
Less heat is produced, tool deflection is decreased, and thinner-walled workpieces can be machined using high-speed/low-force machining.
Conclusion
This concludes our discussion of milling machines’ accuracy and other relevant topics. The machining accuracy of milling can be increased in several ways.
The staff must choose the precise tools and monitor the accuracy of tools and machine tools by the specific processing technology to somewhat guarantee the correctness of the workpiece.
I sincerely hope you found the reading to be enjoyable. If so, please share your thoughts. Thanks!