Disclaimer: As an Amazon affiliate, I may earn a small percentage from qualifying purchases. This is at no extra cost to you. Learn more here.
Last Updated on May 31, 2025 by Larry Edwards
When it comes to the subtractive machining process, the most common machines found in workshops are lathes and mills.
They both work to remove material from a workpiece. However, both of these machines have unique functions and purposes which differentiate them from each other.
This lathe vs. milling machine article will help you understand the differences between the two and under what situations each machine may come in handy.
What is a Milling Machine?
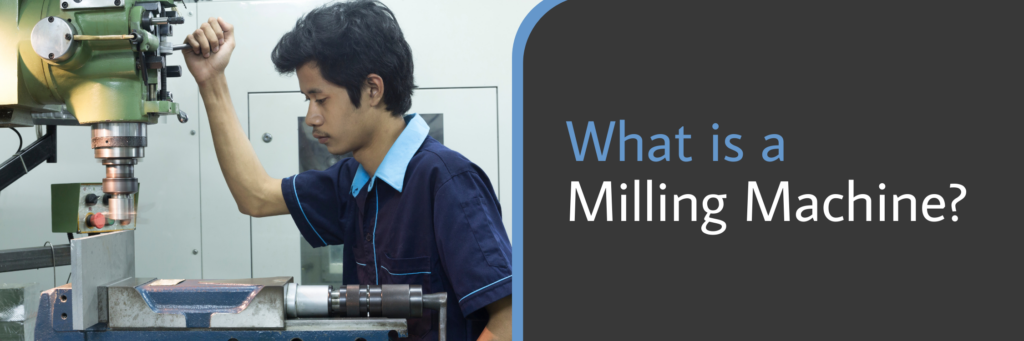
Milling machines are popular with machine shops because of their versatility. Their common operations usually involve metalwork and woodwork, especially when it comes to prototyping.
Its cutting tool has several blades or points, allowing it to work with more complex shapes. The blades in the cutting tool allow for high-precision cutting.
Milling machines have model types that fall into two categories based on their motion: face mills and end mills. A face mill works with the cutting action around the outside of the cutting tool.
On the other hand, an end mill utilizes a cutting action across the circumference of the cutting tool.
There are many types of milling machines. However, the most common ones are the vertical mill, the horizontal mill, and the CNC mill.
Compared to lathes, milling machines are much taller. Their vertical construction allows them to occupy less space and allows them to be easily positioned in smaller workspaces.
Manual milling machines used to be known as the epitome of versatility when it came to these cutting tools. However, when the CNC milling machine was introduced, it gave way to the high-speed manufacturing industry.
How Do Milling Machines Work?
A milling machine moves in three directions to achieve the desired shape for your workpiece. The cutting tool is the one that moves to cut around your stationary workpiece.
You will start by attaching a rotating multi-bladed or pointed cutting tool to the machine’s tool post, depending on the milling process you’re going for.
If your multi-bladed cutting tool moves along the X-axis, it goes left and right. The Y-axis goes in and out while the Z-axis travels up and down.
The workpiece is fastened onto the table of the machine tool. Then, the rotating cutting tool moves around the stationary workpiece to remove material.
What is a Lathe Machine?
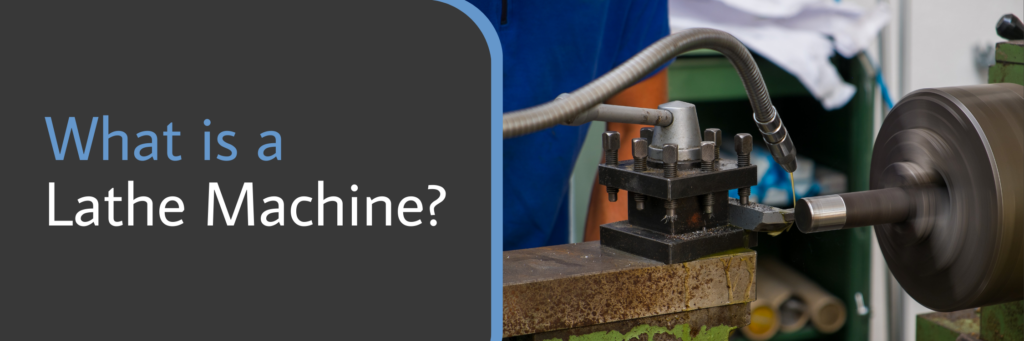
Lathe machines often resemble a whole workbench, occupying more space than milling machines. It also has nearly a dozen parts that help remove material from the workpiece.
Unlike milling machines, a lathe machine works with a single-bladed cutting tool and a rotating workpiece to get the desired product. The workpiece is brought close to the cutting tool to remove any material from it.
There are also many types of lathes. However, the three most common ones are the engine, turret, and CNC lathe.
Engine lathes are primarily used for metalwork. It’s commonly used for processes like drilling, reaming, and boring.
The turret lathe machine is a manual lathe machine with a hexagonal turret. This part, along with the other lathe-cutting tools, is used for several different functions.
A CNC lathe uses a computer program to get the results of engine lathes. CNC turning and machining lets you automate machine tools to replicate a single project easily and precisely.
How Do Lathe Machines Work?
Unlike milling machines, lathes work with a stationary cutting tool. The single-bladed cutting tool is securely placed in the machine’s tool holder or post.
The cross slide helps the single-bladed cutting tool post along the flat surfaces of cylindrical parts or along the direction of the X-axis. Then, the tool is worked across the Z-axis to remove material.
The workpiece rotates against the cutting tool at high speed to remove excess material.
The single-bladed cutting tool produces a round part at the end of your workpiece. Given that it’s a large machine, it lets you work on longer pieces, like shafts, machining them to the proper shape and size.
Like CNC milling machines, A CNC lathe rotates the workpiece against the cutting tool to get the shape needed.
Its machining principle is the same as manual lathes but can easily replicate what you need done across multiple workpieces.
Milling Machines vs. Lathe Machines: Comparison Guide
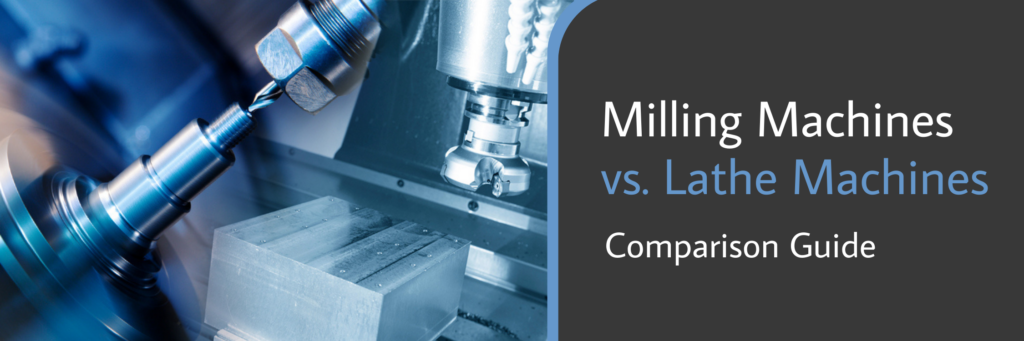
While these two may have the same machining principle, their main difference lies in how these two machines interact with your workpiece.
Here’s a comprehensive guide on the differences between a lathe vs. milling machine.
Purpose and Use
The primary difference between these two machines can be found in their main purpose. After all, machining a workpiece can vary, and there’s no single way to do it.
Lathe machines are best suited for machining cylindrical parts. Since the workpiece rotates for lathe machining, you can best use this machine for boring, facing, drilling, turning, and more.
Threading is another function that’s exclusive to lathe machines. It allows the single-bladed cutting tool to machine your workpiece’s internal and external threads.
On the other hand, milling machines can work with almost any workpiece, making them more versatile than a lathe, thanks to their multi-bladed cutting tool.
Besides being able to do the basic lathe operations, it can also work with a block or roughcast workpiece. Milling machines are best for milling, contouring, drilling, and more.
Accuracy and Precision
During operation, lathe machines involve rotating the workpiece onto a stationary cutting tool, while milling machines involve rotating a stationary workpiece against a moving cutting tool.
With lathes, your rotating workpiece is clamped onto the device, giving you more control of the workpiece.
It’s recommended to work with a CNC lathe to get maximum precision and accuracy for your workpieces. However, a manual lathe machine can also do a great job at a lower price.
It has a tool post that can hold up to 6 cutting tools at once to help you nail the precise shape you want out of cylindrical products.
On the other hand, a milling machine uses a rotating cutting tool that moves across the different axes. The multi-bladed cutting tool allows you to approach a workpiece in different orientations.
A CNC mill is best if you need constant accuracy and precision for many workpieces. It’s highly recommended, especially if you require a huge production of a single material.
Materials and Tools Used
Lathe and milling machines have different cutting tools that help remove material from your workpiece. However, specific tools may be exclusive to a lathe or a mill.
As mentioned, a lathe machine needs more than a dozen parts to work on a single material. Features, like the jaw chuck and magnetic chuck, are all clamped onto a mounting device on the bed.
It uses single-point tools to face, groove, bore, and thread a workpiece. They usually work to shape and smooth out the edges of a long workpiece.
On the other hand, milling machines work with multi-pointed or bladed cutting tools and a worktable for the workpiece to be clamped on.
There are numerous cutting tools available for various processes. The most common are end mills, fly cutters, face mills, and ball cutters. Most are bought with the machine, which helps make it more versatile.
For CNC milling, your workpiece and tools are automatically positioned according to what you’ve programmed into the software. All you have to do is the initial setup.
Cost Comparison
A lathe machine initially has a high cost, especially since it’s a large machine and requires a lot of cutting tools, depending on the model you invest in.
The good thing about a lathe machine is that you don’t always need a CNC lathe to get the best results. A manual lathe is more affordable than a CNC lathe and can also get the job done.
Unlike lathe machines, a milling machine is generally more affordable and capable of various processes. Any additional cost mostly goes to the maintenance of the device.
However, investing in a CNC milling machine is recommended, especially if you work with many products and bulk orders. It helps ensure the accuracy and repeatability of your work process.
It’s usually recommended to have both machine tools if you’re working with a lot of material. However, if you can only afford one, it’s best to base your choice on what you work with.
Frequently Asked Questions
You might have more questions about lathe and milling machines.
I’ve gathered the common questions to help you further understand them and find the right machine for you.
Which is Better: A Milling machine or a Lathe?
While they’re both used to remove material from the workpiece, they do function differently. One machine can be better for a specific process or material.
The milling machine is known for its versatility and affordability, making it the preferred option of many manufacturers, especially those who work with different shapes.
However, if you usually work with cylinders and extended objects, it’s best to invest in a lathe machine.
What are the Advantages of a Milling Machine Over a Lathe Machine?
A milling machine would have a slight advantage over a lathe because of its versatility. Its capabilities are virtually endless since it can work with complex shapes.
Its affordability also makes it more accessible, especially for small businesses and those starting in the industry.
However, it’s not as efficient as a lathe machine when crafting with cylinders and long objects.
Can Milling Be Done on a Lathe?
Most lathes are designed to perform SOME milling processes. These are mostly restricted to drilling processes.
After all, milling machines create tools for lathe machines and vice versa. They tend to work together in the machining industry.
However, having a separate milling machine is still best, especially if you often need its functions. The build of a lathe is also designed specifically for more extended materials.
Which is Better: CNC Lathe or CNC Milling?
Computer Numerical Control, or CNC machines, use software and computer programs to remove material from the workpiece. CNC machining is generally more expensive compared to working with manual machines.
Working with a CNC machine depends on your operation as well. However, they’re best used for processes that work with tight tolerances and require a very high level of precision.
It’s usually better to work with a CNC milling machine than a manual one. CNC mills can better guarantee accuracy and efficiency when working.
CNC lathes, on the other hand, aren’t usually needed unless you work with A LOT of materials. Manual lathes are good enough for smaller, less precise projects.
Final Verdict: When Should You Use Mill vs. Lathe Machine?
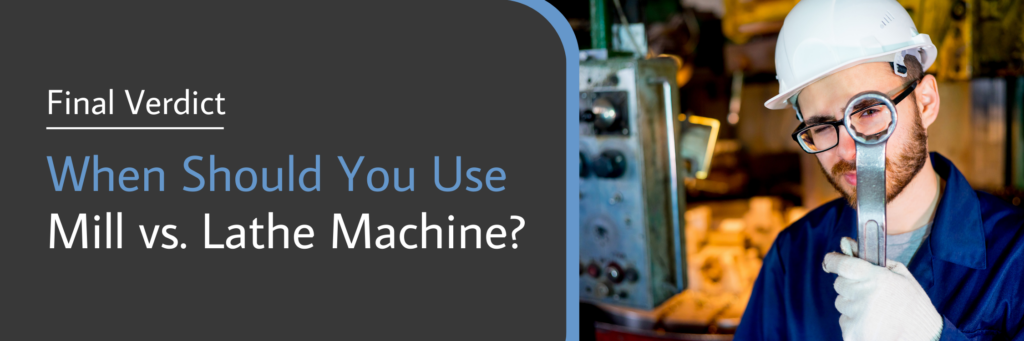
Both lathes and mills are essential machines in the manufacturing industry. A machine shop uses each cutting tool to provide materials needed for construction and industrial production.
However, choosing between the two would depend on your desired specifications and the materials you work with.
You might prefer one machine over the other for your projects, so it’s important to know their differences.
Use a milling machine if…
- You work with peripheral milling and occasional grooving
- Your workpieces need to have a complex shape
Use a lathe machine if…
- You work with large orders of screw cutting
- You work with more cylindrical parts
Conclusion
At the end of the day, both lathes and mills are essential machines in the manufacturing industry. They’re used to remove material on your workpiece, whether you’re working with tough metals or wood.
While they may have many differences, they can both create tools and parts for various industries.
Now that you’re familiar with their differences, you can easily choose between these machine tools for your machine shop.