Disclaimer: As an Amazon affiliate, I may earn a small percentage from qualifying purchases. This is at no extra cost to you. Learn more here.
Boring is really an easy procedure if enlarging an existing hole is the only purpose. And we don’t have to worry about other parameters of the tool. But, when you have to think about a particular size with tight tolerance, everything matters. It’s important to know all about how to use a boring bar.
From boring bar selection to chip evacuation, everything should be accurate and precious. That’s why they say; it’s good to have little OCD problem if you want a precise boring on the lathe.
For a flawless performance in the boring process, knowing the use of the boring bar is important. Today’s article is all about using a boring bar on the lathe.
You can read also:
Beginner’s guide to the metal lathe
How to measure lathe swings
Now let’s go with the main topic.
Using Boring Bar on Lathe
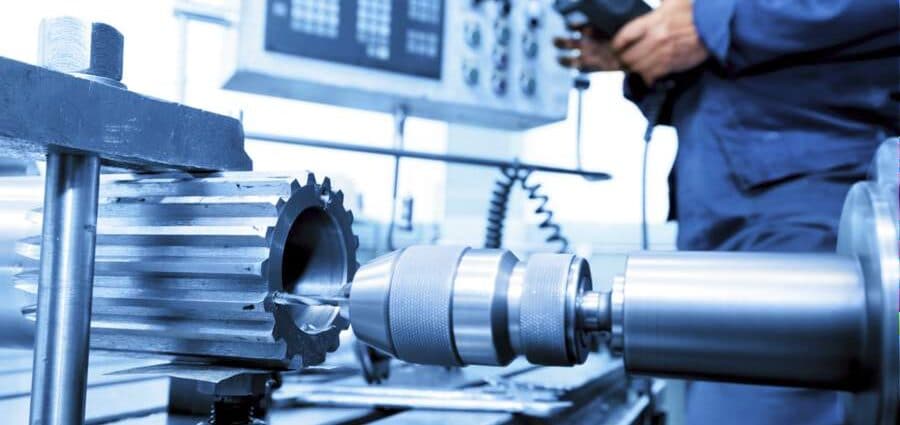
Boring is a kind of basic lathe operation. You can do this with a micro lathe if you wish to. For a successful operation following a few procedures is a must. Hence we are going to talk about the procedure of using a boring bar on the lathe.
Step 1: Selection of Boring Bar
There are three types of boring bars with their own specifications and benefits.
High-Speed Steel (HSS)
HSS is cheaper and tougher. It can be easily re-tipped on a standard grinder and honing stone if the cutting edges wear.
Brazed Carbide Boring Bar
It can cut 2.5-5 times faster than HSS. That means it can tolerate much more heat. Brazed carbide has 2.5 times more modulus of rigidity than steel. But when its cutting edges wear, this type of boring is either reground (which is very difficult) or discarded.
Indexable Carbide Boring Bar
It is like HSS but, when the radius of cutting edge has a smaller corner, a better surface finish is ensured. Also, it produces a more accurate bore size. While cutting edge with a large corner radius is good for roughing.
Hence choose the perfect boring bar according to your operation precision. Stiffness is the key to the boring process. So for better stiffness, using a bar with the largest diameter and shortest extension length is a perfect choice.
Step 2: Measurement of Boring Bar
Determining the accurate measurement of the boring bar is also necessary while using a lathe machine. Because requirements vary from product to product. Hence choosing the perfect size of the bar will lead to a precise result.
Measurements can be done using several tools:
- Dial or Digital Calipers
- Small Hole Gage
- Gage Pins
- Bore Gages
- Telescoping Gages
Step 3: Setting Up the bar
Here are the steps for setting up the bar:
Orientation
Generally, boring bars do not have alignment flats on them. So orienting the top surface of cutting edge parallel to the XZ plane of the lathe is necessary.
There are three possible orientations. These are- negative rake, neutral, and positive rake. Among these three, neutral is the safest. But if you want to try any of the other orientations, you have to set the tooltip on the vertical spindle centerline.
Make sure that you have provided adequate cutting tip clearance.
Cutting weaker materials like aluminum and plastics, it the best to use positive rakes. And to cut stronger materials like higher strength steels, use negative racks.
Height
Height, another considerable parameter while setting up a boring tool on the lathe. Choose a boring bar with a height that is adjustable enough. Which means, as close to the vertical spindle centerline as possible.
While setting up the bar, be very watchful. Because, if the boring bar is not on the vertical centerline, it will surely fail to match your desired size. You will not only regret the wrong operation but also damage the bar permanently.
Step 4: Cutting Parameter Selection
Here are the factors you need to consider before parameter selection:
Cutting Speed
For boring bars, preferable cutting speed should be equal to half of the computed value. But if the tool life allows, you can always work with a limited higher speed than the typical value.
Depth of Cut
Like cutting speed, depth of cut is also an important parameter for the boring bar. In a lathe machine, for the boring bar, it is twice the corner radius, which is considered as the maximum safe depth of cut.
Depending on the material it is said that 0.1-0.2 mm depth of cut is the safest. And around 0.002-0.005 mm is the minimum depth of cut, considering the material.
Note that, below the minimum depth of cut you will get a very inconsistent size and finishing. Because the tool transition remains constant between cutting and smearing.
Feed Rate
One-quarter of the corner radius is the maximum feed rate for a boring bar.
Conclusion
For a successful and precise operation, knowing a few parameters about the tool before starting, is always helpful. It also makes your entire operation much more comfortable.
Hope this article will help you whenever you try to use a boring bar on the lathe.