Disclaimer: As an Amazon affiliate, I may earn a small percentage from qualifying purchases. This is at no extra cost to you. Learn more here.
Last Updated on July 1, 2025 by Larry Edwards
Which traditional drilling tools—carbide or HSS—are superior? And how are these tools differ from each other?
The superiority of HSS and carbide turning tools is still up for dispute among professionals. The answer can be quite controversial, depending on whom you speak.
There is no quick solution because several variables are at play, including tool size, drilling depth, needed material removal rate, tool life, cycle time, and cost, among others.
To help the user understand when to utilize each, we felt it would be helpful to talk a little bit about them. I will explain the distinction between HSS and carbide drills.
In this article, I’ll go over all the benefits and drawbacks of using carbide and HSS drilling tools so you can decide which is best for you.
KEY TAKEAWAYS
- HSS or HS is a group of tool steels frequently used as a material for drilling tools. Power-saw blades and drill bits frequently include it. HSS drill is preferable to the more conventional HSS tools used often during the 1940s in that they can endure higher temperatures without losing their temper (hardness).
- In nearly every application, carbide drills perform superbly. Since they produce the most precise and clean cuts, they are among the most used cutting tool types. This drilling tool is renowned for getting the job done, whether you are cutting plastic, wood, steel, hardened steel, or even titanium nitride.
- Importantly, the higher hardness of carbide tools makes them appropriate for low-volume manufacturing since they make it possible to mill materials with a potential hardness of 70 HRC or higher. Due to their durability and affordability, HSS drills have a wide variety of applications, from portable drills to CNC machining in small batches.
What Are High-Speed Steel (HSS) Tools?
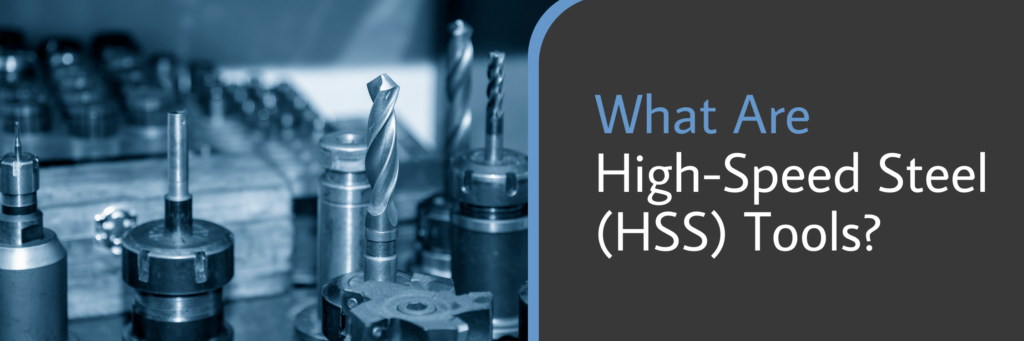
HSS is a group of more than 40 tool steel alloys made of carbon steel and iron that have been alloyed with tungsten or molybdenum at a rate greater than 7%.
The minimal cobalt needed to make carbide milling cutters is significantly less magnetic than HSS.
Regarding multi-toothed form cutters like gear hobbing cutters, milling cutters, and broaches, HSS remains the best and most affordable option.
HSS is employed as the material for cutting tools and machine parts in complex high-speed machining applications.
Their ability for metal cutting speeds 3–4 times quicker than conventional high-carbon steels is how they got their name.
HSS can resist greater temperatures, up to around 650°C, without losing their hardness because the alloying components increase the temperature at which tempering occurs.
HSS end mills are frequently used in drilling small diameters or deep holes because the material’s ability to endure cutting force is a benefit despite its inherent cutting speed limits.
They are easily moldable in a soft condition and a frozen state. Also, they can be reground, allowing additional tool life before being thrown away.
Their extraordinary hardness, abrasion resistance, and resistance to softening at increased temperatures are their main characteristics.
As technology advanced, these tools’ appearances also got better. Here are the pros and cons of using High-Speed Steel tools:
Advantages
- An HSS drill is less expensive than drills made of carbide
- This tool steel can maintain an edge significantly sharper than drills made of carbide.
- An HSS drill can be used to reduce materials that carbide drills cannot reduce.
- Easier sharpening process than carbide
- Higher speed cutting reduces production cycle times
- Compared to carbide, the HSS drill is easier to form, enabling more unusual shapes and cutting edge.
NOTE: TiN coating can increase drill costs by 30 to 50% depending on size and batch quantity, and coated drills can achieve a 30-100% increase in cutting speeds.
Disadvantages
- Although HSS tools are less expensive, they degrade significantly more quickly than carbide.
- HSS tools can only be sharpened a few times before compromising the device’s stability; therefore, even if the edge may be sharper, HSS tools need to be replaced more frequently.
- It will not be effective with some high-hardness alloys.
- The requirement to change drills frequently due to HSS tools’ decreased endurance could negatively influence production output.
- HSS tools do less well in the production of high-quality surface finishes.
NOTE: HSSE tools are highly qualified because they are made from a combination of tungsten carbide, vanadium, and more cobalt.
What Are Carbide Tools?
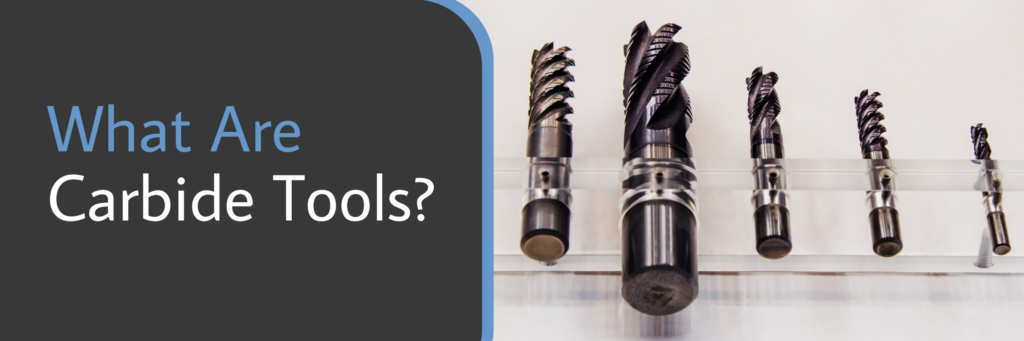
For the past few decades, Carbide Tools and Inserts have been the most frequently used drills in the machining industry.
However, have you ever pondered what carbide is and why carbide tools are so well-liked?
Carbide is a chemical compound made of carbon and an element that is less electronegative than carbon. Broad categories of carbides include:
- Metal carbides are formed when less electronegative metals such as tungsten, titanium, cobalt, tantalum, or vanadium are combined with carbon.
- Carbides made of less electronegative non-metals, such as silicon, calcium, or boron, and carbon
Cobalt was a vital inclusion because it maintained the particles’ cohesiveness.
Metal carbides are employed in metal cutting, drilling, grinding, abrasives, and polishing tools because of their hardness and resilience to high temperatures.
Carbide is used in various cutting applications, from drilling to face milling. It is frequently used when machining cast iron, plastics, and other nonferrous materials.
Consider these benefits and drawbacks of utilizing carbide tools:
Advantages
- Compared to HSS tools, carbide tools can be worked at roughly 6–8 times faster cutting speeds.
- Carbide tools are stiff because Young’s modulus of elasticity is three times greater than steel’s and has higher wear resistance.
- Machines for workpieces and parts that use carbide tools produce high-quality surface finishes.
- Tools made of carbide have high abrasion resistance.
- They are highly resistant to thermal deformations and catering.
Disadvantages
- Honing carbide tools or putting an edge on a productive carbide-cutting tool is difficult.
- It is less economical since the price of a durable carbide tool is substantially more than that of a high-speed tool.
- The internal strain of the carbide tools tends to shape up, restricting their forms and number of cutting rims while still utilizing extremely sharp cutting blades.
- The tensile strength is significantly reduced if high-speed tools are used in opposition.
- Carbide tools fail more frequently than high-speed ones because they are more delicate and brittle.
History of Carbide and High-Speed Steel End Mills
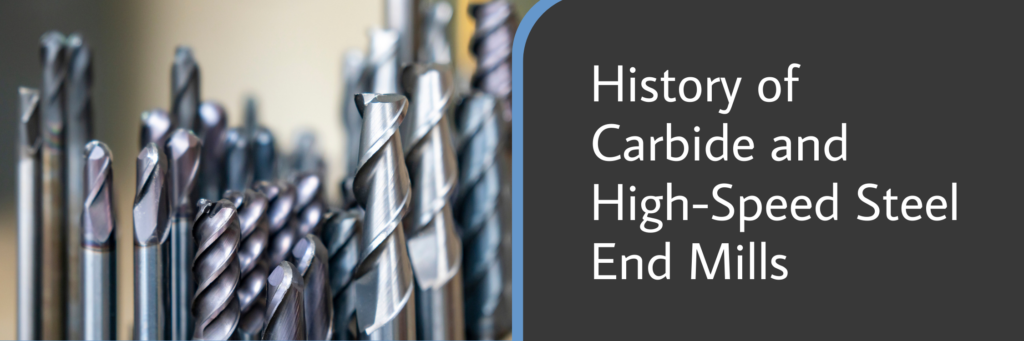
The Bethlehem Steel Company’s experiments at the turn of the 20th century under the direction of Frederick Winslow Taylor and Maunsel White are credited with creating HSS.
The first officially recognized “HSS” alloy debuted in 1910.
Due to resource shortages and rising costs brought on by World War II, molybdenum-rich high-speed steels were developed by 1930 and have been used since then.
Cobalt was added to high-speed molybdenum steels to give extra heat resistance and hardness.
The German manufacturer Friedlich Krupp started offering items made of cemented carbide while tungsten began to be replaced by molybdenum in HSS alloys.
Several Japanese manufacturers and General Electric in the United States contributed to the advancement of technology.
Since carbide’s quality has rapidly improved over the past few decades, it has been used in CNC machining at an increasing rate.
Today, with a few exceptions, most cutting applications choose carbide over HSS.
High-Speed Steel vs. Carbide: Main Differences Explained
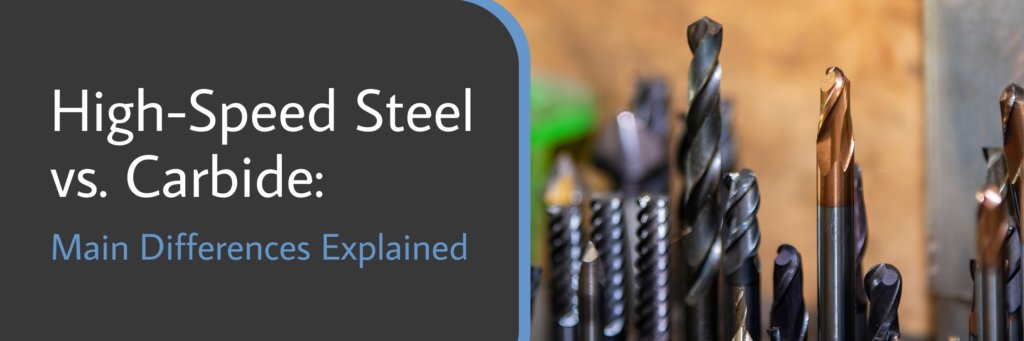
Depending on your particular machining needs, the differences in the tolerances and efficacy of the two materials can greatly impact your processes.
Here are the distinctions between tools made of HSS and carbide to make it easier for you to select the appropriate tools for your next cutting process.
Applications
It makes sense to be concerned with the machining process outcomes, particularly if the project is significant.
For any tool operator, precise, clean, smooth cuts are essential. If you utilize carbide-cutting tools, all of these are simpler to accomplish.
Carbide is appropriate for specific applications because it is stronger than HSS. Furthermore, it can withstand high temperatures; therefore, overheating is not harmful.
You can now concentrate on cutting accurately as a result. Also, it will guarantee a precise and clean cut.
The fact that carbide does not lose its sharpness over time would be beneficial. This eliminates the possibility of a dull blade spoiling your work.
Ease of Use
We already know that a carbide blade will last longer than a steel one. This suggests that carbide tools last longer than steel ones. It implies that they require regular re-sharpening.
These units will only become worn out quickly if you use them on sturdy fabrics.
The process of sharpening is rather simple, which is good news. It still takes time and effort for the user to sharpen a tool.
On the other hand, carbide tools require less frequent sharpening and last longer. To guarantee the best possible product performance, check its sharpness routinely.
Once the tool becomes dull, it is time to use a carbide saw blade sharpener. You can make do and sharpen carbide using a slow-speed grinder.
You can also bring the tool to a specialist who has a sharpening machine in their store.
Durability
Tools made of carbide are not only robust but also long-lasting. It increases their adaptability and qualifies them for a variety of materials.
Using carbide to cut drills you are recycling is also a sensible idea. Consider using screws to shape a wooden application as an illustration.
While the limber may be cut with HSS drills, what about the screws? HSS drills have a narrow helix that drills softer materials precisely.
If you come upon a screw that was forgotten, it can shatter. Contrarily, carbide will pass through that screw without even trying to halt.
Carbide units are also suitable for materials like hardwood and comparable applications that produce a lot of dust and debris.
They can effectively cut through dust and particles without endangering the tool. It is recommended to keep the device secure constantly.
Suppose you see too much trash, pause and clean it up. It will guarantee enhanced outcomes and better device performance.
Cutting Speed
Regarding cutting speed, carbide blows HSS out of the water.
A carbide tool may cut 4 to 12 times quicker than an HSS device under similar conditions (depending on the work material and type of process), and the productivity is great.
Slower cutting speeds are used with standard HSS grades. HSS-PM (Powder Metallurgy) was created recently to fill the gap between HSS and carbide tools.
Tool Life
The truth is that while HSS drills may be less expensive, a carbide blade will perform better over time. The balance between cost and durability must therefore be addressed.
You must purchase a new HSS unit if the one you initially purchased only lasts a short while. However, a single carbide chainsaw blade might be a wise long-term investment if it lasts long.
The cost can increase if you choose a carbide saw blade with specific dimensions. Despite this, the cost can be affordable if you want a sturdy and long-lasting tool.
It is critical to emphasize that routine maintenance is necessary for the best possible material longevity. Because of this, it’s crucial to clean your carbide-cutting device frequently.
By doing this, any residue won’t affect the device’s functionality and will increase the risk of overheating, drill breakage, and other problems.
The experts also recommend storing the device securely. That means keeping it safe to prevent accidental cutting and protecting the device from harm when not in use.
Frequently Asked Questions (FAQs)
Here are the frequently asked questions about HSS and Carbide tools:
Can HSS Be Used for Precision Cutting?
For a vast majority of tasks in their machining operations, experts still use HSS drills.
Reamers, Taps, and End mills are particularly useful when precise cuts, deep or tiny holes, or even threads are needed.
Is Carbide More Expensive than HSS?
HSS drills are frequently a good option in “high-mix, low-volume” applications and are less expensive than Carbide tools.
Is HSS Easier to Use Than Carbide?
Regarding the tapping procedure, HSS’s superior toughness to carbide is crucial.
High-Speed Steel vs. Carbide: Which Tool Is Better?
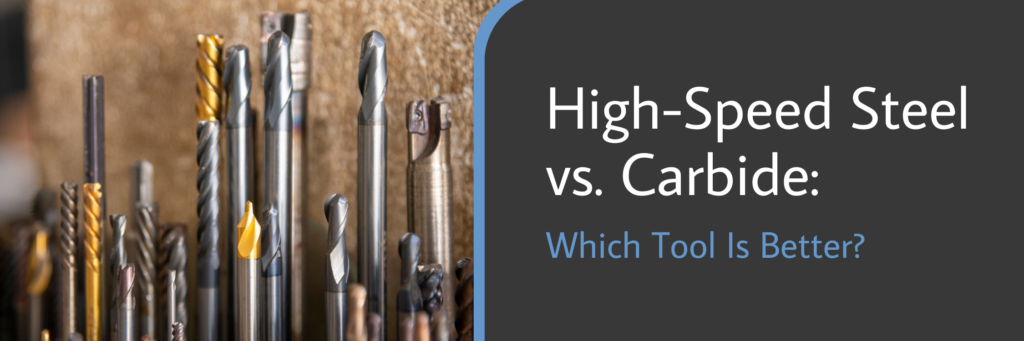
Here are some instances of when you can use each tool:
Use HSS If…
- You like utilizing cheaper tools.
- You need a device that can maintain an extremely sharp edge
- You desire a device that can be utilized to cut down on supplies.
- A tool that is simpler to sharpen is necessary.
- You require a tool that enables more unusual cutting edges and extreme shapes.
Use Carbide If…
- You want a superior choice when working with extremely tough materials like polymers, glass-filled plastics, and cast iron.
- You choose a high heat tolerance that enables greater cutting rates in RPM.
- You require a faster cutting process that shortens manufacturing cycle times.
- It would be best if you had a tool that stays tough even when compressed.
- A longer operating life is desired due to greater wear resistance.
- A tool that produces superior surface finishes to HSS tools is what you desire.
- For either rigid or synchronous CNC machines, you want the proper tool.
Conclusion
As you can see, every tool has unique advantages. In actuality, you can have both in your toolbox.
Some materials can be quickly and cheaply cut with HSS drills. However, carbide is stronger, more resilient, and can handle demanding applications.
The most important thing is to select the proper solution, regardless of your application or operational factors.
I sincerely hope this article has helped you understand which tool to use when and when not.
Ultimately, what matters is what you produce, not the milling tools that help you get there. Use whatever serves your needs and works.